知られざるアライヘルメットの中身 Vol.2【どこまでも重さにシビア。帽体の中に入れる本体の生地は3g以内の精度で製作】
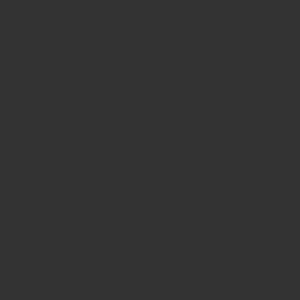
群馬県にあるアライヘルメットの榛東工場は、約50年前からシェルの生産基地として稼働。世界を見据えた開発を目指してスタートし、今は世界中のライダーの頭を護っている。ヘルメットはモデルチェンジの度に生産工程が増え、生産のほとんどで人の手が介するため、生産効率を上げることが難しい。しかし、護ることへの探究心と、そのための細かい技術の積み重ねが安全性を向上させ続けると信じる姿勢はこれからも変わらない。
●文:ミリオーレ編集部(小川勤) ●写真:長谷川徹 ●BRAND POST提供:アライヘルメット
知られざるアライヘルメットの中身 Vol.1【人の目と手に委ねられている、モノづくり】はこちら
いくら剛いヘルメットでも重かったら仕方がない
工場内を見学していて驚くのは、いたるところに量りがあり、重さをチェックする人がたくさんいることだ。強度と軽さ。アライヘルメットは、相反するこの2つを追求し続けている。そしてシェルの内側と外側に強度のある素材を用い、中に柔らかい素材を用いたcLc構造を生み出した。
「持って軽いヘルメットも、被った時に重かったらしょうがないんですよ。重心は下にあれば重さを感じにくい。人間の首は常に5〜6kgの頭を蝶番のように受け止めていているんです。重心に近いほど重さを感じないから、下までしっかりつくった方がいいんです。
しかし、頂点は重くない方が良いから特殊な繊維素材を使っています。これは防弾チョッキなどにも使われる素材で20世紀最強の素材とも言われています。
難しいのは、おでこの部分。衝撃を吸収する面積が狭く、だからと発泡ライナで厚くしてしまうと前傾姿勢を取った時に前が見えにくくなってしまう。そんなところは発泡ライナの硬度を細かく変えて対応するんです。そうすると耐えてくれるから、無駄な厚みを出さずに済むんです」と、アライヘルメット執行役員常務の原田重行さん。
帽体の中に入れる本体の素材は3~6g以内の精度
1つのヘルメットには本当に様々な素材が入っている。そのひとつにスーパーファイバーベルトがあり、その素材はアライヘルメットの自社製だ。シートベルトをつくる機械で縦糸の本数や幅、糸の太さや特性を変えながら最適な生地をつくる。自社で製作することで、「ここは、もう少し強度がほしい」っとなった時にも迅速に対応できるようになっている。
そして、帽体の中に入れる本体の素材の重量幅は3~6g。樹脂を吸うとこの誤差は約2倍と大きくなるため、かなりシビアだ。全部の材料を検査し、重さを量る。メーカーからの材料も来た段階ですべて検査し、裁断してからも計測。その作業がすべて終わるとようやく素材同士を合わせる作業になる。
金型に入れた時にシワにならないよう、素材自体を数ミリ単位で合成していくのだ。
これまでの素材を金型に入れ、熱を加えて成形していく
そしてここまで製作されたものをいよいよ金型に入れ、熱を加えて樹脂で固める。数十種類の素材を組み合わせたものを金型に入れるこの作業は熟練の腕が必要。ツルツルの金型に材料を入れると当然滑ることもあり、ここで数ミリでも素材同士がズレたり、シワになってしまうと、各部の欲しい性能を引き出せないからだ。
シェル成形の部屋に入ると、熱気が凄い。金型が50台もあるのだからそれもそのはず。ひとつの金型で1日20個つくる。1人4つの金型を担当するというが、熱は熱を引っ張るから、端と真ん中の金型では温度が異なる。ちなみにこの日見せていただいたヘルメットは、100度以上で10分以上焼くのだという。
もちろんヘルメットの種類やサイズによってはもちろん、季節や部屋の入口に近い場所と奥の方でも金型の温度は異なるため、職人たちの長年の経験から生み出される正確な判断が必要となる。夏場は部屋の温度が40度を超えることもあるというから大変だ。
ちなみに金型から出てきたばかりの帽体に触らせてもらったが、薄いところはなんとか触れるが、厚いところは触れないほどの高熱を有していた。でも職人達はすべて素手で帽体を掲げて目視でチェックし、重量を細かく計測していた。
レーザーロボットでカットして、乾燥させる
金型から出てきた帽体を、6台のレーザーロボットがカットしていく。見ていて不思議なのは、レーザーロボットは順不同に形の異なる帽体を掴み、その帽体に合わせた箇所を正確にカットしていくところ。
聞くと、ロボットが帽体を掴んだ瞬間にどのヘルメットかを判断しているのだという。すべてのレーザーロボットに全ヘルメットのデータを入力。ひとつのヘルメットに対し数百か所のポイントを覚えさせ、カットする。
ちなみにこうした製作過程ででたガラス繊維の端材は、専門の業者に委託しセメントの助燃剤として再利用されている。アライヘルメットはサステナブルという言葉がうたわれる以前よりももっと早くから環境を意識した試みも実施しているのだ。
カットが終わった帽体は、100度の乾燥炉に3時間入れて樹脂とFRPをさらに馴染ませる。乾燥前のものを叩くと樹脂っぽい「ペコッペコッ」という柔らかい音だったが、乾燥後は「カーン、カーン!」とまるで金属を叩いているような硬い音に変わった。
最初に見たフワフワの仮成形品が様々な工程を経て、帽体に変わっていく。それは量産という一言で語れない、とても繊細な作業の積み重ねだった。
全数、手作業で厚みを計測
乾燥させたヘルメットは各部のバリを取り、全数、全箇所の厚みを計測。薄いところには緑で印をつけ、厚みに応じて高強度の素材を貼って補強していく。メーカーによっては強度試験をする場所だけを厚くしているものもあるというが、アライヘルメットは全体の厚さにこだわっている。
『かわす性能』はヒットした部分だけでなく、かわしながら様々な箇所で衝撃を逃すため、どこが当たってもいいように、全体の厚さを厳しくチェックしていくのだ。ちなみに同じ検査を再度本社でも行うという念の入れようである。
とにかく磨いてクオリティを上げていく
塗装前の帽体には重量が書いてあり、見せていただいたのは688.8gだった。塗装の重量も規定値内で仕上げられ、この場合だと例えば塗装済ませて790gだと不良品になってしまうのだという。数グラムの精度をここでも求める。
ここまできた帽体は、製作者の名前もスタンプされ、成形した人、窓をカットした人、補修した人、検査した人など、誰が何をしたかがすべてわかるようになっているのである。
下地づくりは、まずはファンデーションのような役割となるピンクのウレタン系のサフェーサーを吹く。これはFRPと塗装をくっつきやすくするための役割。それを磨いてから次は柔らかめの白のポリエステル系のサフェーサーを吹き、チェック用の細かい墨を飛ばして、再び磨く。墨がきれいになくなるまで、丁寧に磨く。
強度と軽量化のためにアライヘルメットでは樹脂を極力少なめにしているので、この段階での出来上がりは表面がややザラついている。そのためにこうして何度も磨いたりチェックをして、塗装前のベースをつくっていくのだ。
下地ができたら次は塗装ブースへ。室内をインバーターで調整し、外に空気を引っ張ることでホコリの混入を防いでいる。ちなみに冬は温度管理しないと塗装の硬さが変わってしまうため、暖かい空気を入れるのだという。
塗装が済んだら、デカール貼り。デカールをぬるま湯で伸ばしながら皺にならないように貼っていく。平均すると1人、1日8個程度(アライ榛東工場)しか貼れないとても繊細な作業だ。デカールを貼り終えた帽体は、高温で数時間、乾燥炉にかける。
そして再び磨いてクリアを吹き、ホコリなどをチェック。ホコリがあるとその部分をペーパーで磨き、さらに艶出しを行う。こちらも全数検査を行い、さらに本社で組み立て前にも同じ検査を行う。
ここまで行い、ようやく帽体は完成し、内装を組み込んでいくのである。
ちなみに1つのヘルメットをつくるのにのべ30日かかるというから、どれだけの手間がかけられているかがわかると思う。
技術だけでなく、人の経験や勘、実際に被るライダーへの優しさや思いやりが大切なモノづくり
バイクに興味を持ったらヘルメットを選ぶのは当然のこと。でもそこで何を選ぶかはとても大切だ。今回の工場見学で職人の仕事に感銘を受け、そのことの大切さを痛感した。ヘルメットづくりの奥深さに吸い込まれ、もっと多くの人にこのモノづくりを知ってほしいと思った。
そのモノづくりは非常に複雑だ。人の経験や勘に頼る部分が多く、それこそが非常に高度な職人技だった。手づくり=古くさい、そんな風に思う人もいるかもしれない。しかし、人の手でしか生まれないイノベーションを約70年も追求し続けるのがアライヘルメットなのだ。
『頭を護る』こと、そのハードルはバイクの進化、タイヤの進化、スピードの向上などにより上がり続けている。しかし、アライヘルメットは諦めない。粘り強く、試行錯誤を繰り返し、どこまでも自分達に厳しく向き合う。厳しさの中にもライダーへの優しさや思いやりも忘れてはいないアライヘルメットのモノづくり。護るために何ができるか、職人の「目」や「手」がそれを探し続け、昇華させ続けているように感じた。
※本記事はアライヘルメットが提供したもので、一部プロモーション要素を含みます。※掲載内容は公開日時点のものであり、将来にわたってその真正性を保証するものでないこと、公開後の時間経過等に伴って内容に不備が生じる可能性があることをご了承ください。※特別な表記がないかぎり、価格情報は税込です。