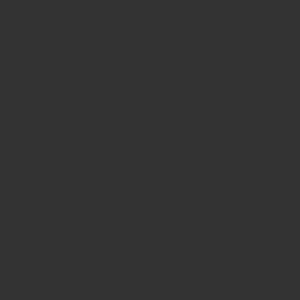
iB井上ボーリングが積極的に展開してきたICBM®技術。内燃機ファンの間ではもはや当たり前であり、“高性能な技術”としても認識評価されている。本記事ではこのICBM®技術にあらためて注目。その特徴を未体験のユーザーにお知らせできればと考えている。
●文/写真:たぐちかつみ(モトメカニック編集部) ●外部リンク:iB井上ボーリング
アルミスリーブは圧倒的な放熱性を誇る
iB井上ボーリング(以下iB)が取り扱う内燃機加工修理の中で、とくに、大きなシェアを占めているのが“空冷エンジン”のシリンダー。
減らないアルミシリンダー「ICBM®」の主力機種でもあるカワサキZ2/Z1はもちろん、ホンダCB750やヤマハDT-1にカワサキトリプルなどなど。とくにカワサキトリプルは、大型モデルのH1/H2に限らず、ミドル系シリーズモデルへの施工依頼も数多くある。
1980年に登場したヤマハRZあたりから、市販車も水冷エンジンへと移行していくが、加工依頼は1960〜1970年代モデル用が圧倒的に多いそうだ。
空冷のエンジンは、冷却フィンの造形が美しくモデルごとに特徴があり、水冷エンジンのノペっとした印象とは大きく異なっている。
造形が美しい冷却フィンの空冷エンジンはとても魅力的だが、やはり冷却性能という点では、水冷のエンジンに分があるのは認めざるを得ない。シリンダー全体を均一に冷やすという点で、水冷式には圧倒的なメリットがある。
冷却性能という点ではやや苦しい空冷エンジンだが、もともとは“鋳鉄の塊”だったので、アルミシリンダーの中に鋳鉄のスリーブが圧入(あるいは鋳込み)されるようになったことで、冷却フィンを介して放熱性は大きく改善されている。
アルミと鋳鉄では熱伝導性に大きな違いがあり、アルミははるかに放熱性が優れている。熱伝導率を数値で表すと、純鉄が67で、黒鉛が潤滑の役割を果たすFCD=球状黒鉛鋳鉄が35前後、それらに対してアルミニウムは204(熱伝導率の単位は[W/mK])となっている。
同じ鉄でも鋳鉄は純鉄より熱伝導率が低く、放熱しにくい素材だとわかる。しかしながら、耐摩耗性が高く、それをコントロールしやすいのも鋳鉄(含有成分のさじ加減で耐摩耗性が変化する)だ。一方で、これがアルミ製になると、熱伝導率は一気に向上し、放熱性が圧倒的に良くなることが理解できる。
実際、シリンダーに限らず電子部品などにも、アルミ製ヒートシンクというシリンダーフィンのような形状を持った部品が放熱のために使われている。一般に入手可能な金属の中では、銀や金と銅に次ぐ熱伝導率を誇っているのがアルミニウムなのだ。
そして、この中では、比較的安価なアルミが放熱性向上のための部品として多用されるのも、当然と言えば当然のことになる。そんな放熱性が唯一の目的ではないが、特殊めっき処理による耐摩耗性の向上や軽量という意味でも優れているため、シリンダースリーブにも、鋳鉄から特殊めっき処理の内径を持つアルミスリーブが採用されるようになっていった。
熱伝導率を元に放熱量を計算で出すのは困難だが、一例としてヤマハSR400のシリンダーをICBM®にしたところ、油温が同条件で10度近く低下した実績もあった。
もちろん計測条件によって結果は変わる場合もある。ちなみに、蓄熱することでも知られるステンレスのSUS304は、タンブラーやポット(魔法瓶)などにも使われているが、この素材の熱伝導率が16.0となっている。鋳鉄素材は、このステンレスと実は変わらない、金属の中でも放熱が良くない素材であることもわかる。
アルミめっきスリーブのICBM®におけるホーニング処理は、プラトーホーニングが標準指定となる。深い谷がオイル溜まりとなり、平滑な高原部分でピストンが摺動する。面粗度計による測定データ。
カワサキZ1用の純正鋳鉄スリーブ(左)とアルミスリーブ(ニッケルシリコンカーバイドの特殊めっき前)。手に持つことで驚くのが、その軽さの違いだ。ICBM®化によって圧倒的な軽量化も達成できる。
潤滑性と滑性。低フリクション性の向上
過去にiBでは、スズキGS750の4気筒シリンダーのうち、内側の2本をICBM®仕様にして、外側1本を純正スリーブのまま、もう1本の外側をiB製削り出し鋳鉄スリーブに変更するテストを行ったことがある。
もちろん4本とも同条件のホーニング処理で仕上げ、一定の距離を走行後に分解して、変化状況を確認したそうだ。純正鋳鉄スリーブと摺動したピストンを見ると、スカート部にはあきらかな縦キズが入っていて、見るからにザラザラしていたそう。
一方、ICBM®アルミめっきメッキスリーブと摺動したピストンは、指で触れてもツルツルすべすべしていたそうだ。指先で触れてみれば、その違いは誰にも明らかだった。
この摺動コンディションの違いは、ピストンスカート部だけに出るものではなく、とりわけ大きかったのがピストンリングにあったそうだ。つまり、ピストンリングの摩耗状態に違いがあった=大きな差が出たのだ。
一般にふたつの物体が摺動する場合、片方の硬度が高まれば、そちらの摩耗は減少するもの。その一方で、摺動する相手側は「摩耗量が増加したり、ダメージを受けたりするもの…」と想像されても無理はないことだろう。ICBM®のめっき硬度をユーザーへ伝えると、前述したような心配を抱く方がいても当然だろう。
ところが、実際この特殊めっきに起こる事態は、それとはまったく逆で、相手のピストンリング(ハードクロームめっきリングが大半)の摩耗も著しく減少させるのだ。
ひとつの理由として考えられるのは、メッキ後の“プラトーホーニング”が大きな役割を果たしていること。オイル溜まりとなる谷が深いながらも、実際にピストンリングが摺動する面が平滑に仕上げられていることによる効果だと考えられる。
それ以上に、ニッケルシリコンカーバイドを主成分にした特殊めっきが、ピストンリング外周に施されるハードクロームめっきとの相性を高めているようなのだ。もともとはドイツのマーレー社が開発した技術で、登録商標名は「ニカジル」として知られている。
iBのめっき処理を含め、マーレー社以外のめっき処理技術はニカジルと呼称することはできず、それ以外の各社のめっき技術は、それをさらに研究開発進化させためっき処理技術と言うことができる。内燃機関の内径=シリンダーへの適用のみを目的として開発されたものなのだ。
熱と圧力を受けつつ、その一方で、潤滑油のなかでの過酷な摺動という、極めて特殊な条件に適合した圧倒的な性能を持つめっき処理技術なのだ。
過去には、この特殊めっき処理技術以外にも、iBではあらゆるめっき処理技術をシリンダーに施し開発に挑戦しているが、8年の歳月を費やしても、十分な性能を持つものが見つからず、けっきょく高価なこのニッケルシリコンカーバイドの特殊めっきを採用するに至っている。
さらにその後は4年ほどを費やし、めっき治具への投資をすすめ、あらゆるシリンダーボアに対応できる体制を構築し、現在の状況になったのが2016年のことになる。現在では、ICBM®仕様への加工納品実績が1000を大きく超えている。「永久無償修理」制度も実施していて、ユーザーからの信頼も獲得しているのだ。
ヤマハSRのシリンダーにのみ刻まれるICBM®のシリアルナンバー。もちろん表示なしも選べる。オーバーヒート対策としてのICBM®も注目されている。ボアアップ時のシリンダーには最適の技術だ。
国産車や外車を問わずさまざまなモデルにICBM®技術が投入されている。各ポート孔がある2ストモデルの機種対応時にはダミースリーブを製作し、ポート形状を確認している。
ICBM®「永久無償修理」制度は、施工済み証明でもあるシリアルナンバー入りカードで管理されている。裏側にシリアルが削られたiBマークの削り出しキーホルダーストラップも付属。
※掲載内容は公開日時点のものであり、将来にわたってその真正性を保証するものでないこと、公開後の時間経過等に伴って内容に不備が生じる可能性があることをご了承ください。
ヤングマシンの最新記事
シグナスシリーズ、20年の歴史を背負うニューフェイス 以前は空冷エンジン搭載のコンパクトな原付二種スポーツスクーターとして人気を博した「シグナスX」だが、水冷の新世代「シグナス グリファス」に交代した[…]
皮脂や汗に含まれる尿素が生地を痛めてしまう ──一般の方が汗でびちょびちょのヘルメットをリフレッシュさせたい場合、どのように行えばよいでしょうか? 「どこが外せるのか、どういうふうに洗えばいいのかは、[…]
発表と同時に発売! マットチタニウムカラーのアヴェニス125など新色×5種 スズキは欧州で、日本でいう原付二種に相当する125ccのスクーター×2車をカラーチェンジ。1車は2022年の現地登場以来(日[…]
鮮やかなブルーでスポーティな外観に 欧州においてスズキ「ハヤブサ」が2026年モデルへと更新された。アルティメットスポーツを標ぼうするマシンは基本的に2025年モデルを踏襲しながら、レギュラーカラーが[…]
「56design NARA」に続く新店舗が北海道に バイクアパレル&ファッションブランド「56design(フィフティシックス・デザイン)」が、北海道札幌市に新店舗「56design SAP[…]
最新の関連記事(iB井上ボーリング)
熱膨張率の均一化によって様々なアドバンテージがある 2ストローク/4ストロークエンジンを問わず、エンジン性能を向上するためには様々な課題や問題がある。特に大きな課題は、“熱膨張率”に関わる問題だ。 「[…]
何よりも高耐摩耗性の実現 圧倒的な耐摩耗性を誇るのが、アルミめっきシリンダーの大きな特徴である。iB井上ボーリングが、アルミめっきスリーブを作ろうと考えた最大の理由は、同社の社是でもある「減らないシリ[…]
現代のめっきシリンダー技術を、往年の名車や旧車エンジンに オイル交換をしっかりかつ定期的に行っていても、長年乗り続けることでどうしてもすり減ってしまうのが鋳鉄シリンダースリーブ。そんな鋳鉄スリーブに対[…]
減らないシリンダーづくりを現実的にした技術「ICBM」 金属表面の硬度を表すひとつの基準にビッカース硬度がある。鋳鉄の硬度が45から、硬いスリーブ素材でも140程度のデータに対して、ICBM®シリンダ[…]
入手困難な旧車のパーツをクラウドファンディング 「群衆/Crowd×資金調達/Funding」という言葉を組み合わせた造語が「クラウドファンディング」。インターネットやSNSを通じて、不特定の賛同者に[…]
最新の関連記事(メンテナンス&レストア)
フレキシブルプラグソケット:スリムな外径で汎用性をアップした、ユニバーサルジョイント一体ソケット 最初は指でねじ込んで、ネジ山が噛み合ってからプラグソケットを使うのが理想だが、雌ネジがプラグ穴のはるか[…]
皮脂や汗に含まれる尿素が生地を痛めてしまう ──一般の方が汗でびちょびちょのヘルメットをリフレッシュさせたい場合、どのように行えばよいでしょうか? 「どこが外せるのか、どういうふうに洗えばいいのかは、[…]
論より証拠! 試して実感その効果!! 世界的に知られるプレミアムカー用品ブランド・シュアラスターが、アメリカのカリフォルニア州ロングビーチで創業したのは1947年のこと。以来、カーシャンプーやワックス[…]
バイクの電装部品のひとつ、レギュレターってご存じですか? こういうの部品です。 車種によって場所はマチマチですが、だいたいがシルバーで、アルミ素材で空冷フィンがついていて、比較的バッテリーに近いところ[…]
メーカー自体が存在しない絶版車のメンテやレストアは難しい 日本のバイクメーカーは今でこそ4社に集約されていますが、1950年代には大小含めて数十社のメーカーが林立していました。第二次世界大戦で疲弊した[…]
人気記事ランキング(全体)
ホンダ「CB1000F SE コンセプト」が鈴鹿8耐で世界初公開! 8月1日より予選が始まった“コカ・コーラ”鈴鹿8時間耐久ロードレース第46回大会のホンダブースにて、CB1000F SE コンセプト[…]
3色すべてホイールカラーも異なる カワサキは欧州でZ650RSのニューカラーを発表。カラーバリエーションの全てが新色に置き換わり、黒ボディにレッドストライプ&レッドホイールのエボニー、メタリックブルー[…]
国内規制に合わせてエンジンを再設計 ホンダのCB750フォア(1969年)の発売と前後して、大型バイクの事故の増加や暴走族が社会問題化し、国内では750ccを超える排気量のバイクを販売しない自主規制が[…]
KOMINE プロテクトフルメッシュジャケット ネオ JK-1623 フルメッシュで残暑厳しい秋口のツーリングでも快適さを保つジャケット。胸部・肩・肘・背中にプロテクターを標準装備し、高い安全性も両立[…]
最小限のカスタムでクルーザーをアドベンチャーマシン化 1200ccという大排気量の水平対向エンジンを心臓部に持つBMWのヘリテイジモデル、R12シリーズ。その新しいバリエーションとして2025年5月に[…]
最新の投稿記事(全体)
秋の浜松はスズキ祭り! 3つのミーティングが開催 2025年のスズキミーティングは、3つのモデルシリーズに焦点を当てて開催される。 9月7日(日) 「KATANA Meeting 2025」 会場:は[…]
作って、触って、攻略する。新感覚のサーキット模型 スマホケースなどの地図柄グッズを手がけるクロスフィールドデザインが、モビリティライフスタイルブランド「レシプロ」の新商品として「レイヤード ランドスケ[…]
国産から海外、EVまで! 圧巻の車両ラインナップを見よ! 総展示台数350台以上を誇る東北最大級のバイクイベント「BIKETOBER FESTA」。新車購入を検討している者から、愛車のカスタムを考えて[…]
RA1250ST パンアメリカ1250ST:オンロードを制するためのニューマシン“ST”登場 アメリカで人気沸騰中のスーパーフーリガンレースでは、公式バイクとして位置づけられ、H-Dファクトリーのサポ[…]
フレキシブルプラグソケット:スリムな外径で汎用性をアップした、ユニバーサルジョイント一体ソケット 最初は指でねじ込んで、ネジ山が噛み合ってからプラグソケットを使うのが理想だが、雌ネジがプラグ穴のはるか[…]
- 1
- 2