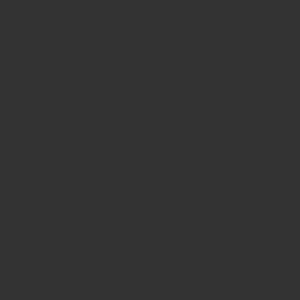
30年バイクに乗り続け、その際は必ずヘルメットを被っているというのに、恥ずかしながら僕はヘルメットがどのようにつくられているのか何も知らなかった。今回、初めてヘルメットの帽体の製作工程を見せていただき、アライヘルメットの工場の職人が世界中のライダーの頭を護ってくれていたのだと思い知った。繊細な手作業と気配り、そして確かな目、機械任せにできない人の技術と匠の力がアライヘルメットの榛東(シントウ)工場には宿っていた。
●文:ミリオーレ編集部(小川勤) ●写真:長谷川徹 ●BRAND POST提供:アライヘルメット
予測不可能な多方面からの衝撃をいかにかわすか
2022年シーズンのMotoGP第9戦カタルーニャGP。スタート直後の1コーナーで中上貴晶選手がクラッシュ。転倒直後にフランチェスコ・バニャイヤ選手のリヤタイヤに顔をヒット。その瞬間にシールドが飛び、自身のバイクやアレックス・リンス選手のマシンにも接触……。
2022年のMotoGP第9戦カタルーニャGPで、中上貴晶選手がクラッシュした際のヘルメット。いま映像を見ても、彼が無事だったのが奇跡といえるだろう。
その時の中上選手が被っていたヘルメットを目の前にした瞬間、鳥肌が立った。無数の傷はもちろん、あごの部分や後頭部に残る大きなタイヤ痕に戦慄が走ったのだ……。一目見るだけで、それは様々な方向から想像を絶する衝撃が頭に加わっていたことを物語っていた。
「パン! パシーン! パシーン!」。アライヘルメット執行役員常務の原田重行さんが、手で思い切りヘルメットを叩く。様々な方向から容赦なく叩く。「我々ヘルメット屋はね、この形状を守らないといけないんです。頭を護るためのこの曲率をね。転ばないのがいちばんいい。でも転んでしまったらライダーを護りたい」と原田さん。
「パシーン! パシーン!」と硬質な音が室内に響き、原田さんの手はヘルメットに当たった瞬間、大きく軌跡を変える。「この形状じゃないとぶつかった時に引っかかることがある。それじゃ、ライダーを護れないんですよ」。そう語る原田さんを前に、僕がこれまで被ってきたヘルメットが思い浮かんだ。何度か転倒したこともある、でも大事に至らなかったことに改めて感謝した。
この日、僕は群馬県にあるアライヘルメットの榛東工場を訪問。「今日見ていただく工程と工場内は、アライヘルメットのノウハウが長年積み重なった特別なものなので、外部の人にはほぼ公開していません。何年も前に欧米の方が見に来て以来かな。だから撮影できることころもほとんどないんですよ……」と原田さん。
中上選手のヘルメットの前後についたタイヤ痕。走行中のタイヤに顔から突っ込んでいくのはとても恐ろしかったと思う。転倒後、中上選手は入院。自身のSNSで2日後に退院したことを伝え、バニャイヤ選手とリンス選手に謝罪。石が当たったことで顔は腫れていたが大事には至らなかった。
どこまでもあるのは『ヘルメット屋のプライド』
いま、ヘルメットには様々な規格がある。そしてそれは国によって異なる。しかし、アライヘルメットは、これらの規格が存在する以前からヘルメットをつくり続けている。
自分の頭をどう護るか? ライダーの頭をどう護るか? アライヘルメットは常にそればかりを考え、そのためのプロダクトを開発してきた。バイク用ヘルメットを手掛ける以前から工業用ヘルメットもたくさんつくっていたが、この2つのヘルメットは根本的に思想が異なる。なぜなら外部の衝撃から護るだけでなく、ライダーの場合はバイクに投げ出され自らが飛んでいく=自身が衝撃となって何かにぶつかるという可能性もあるからだ。
今回の取材のために3種類のファイバーが用意されていた。その3種類を手で折ってみると……。
「ヘルメットっていうのは規格以上に色々なことがあるんですよ。でも、とにかく護りたいんです。そのために歩むべき道を進み、常に探求している。護ることへの誇りをスタッフ全員が持っているんです。そして手づくりだから生まれるプロテクションがある。護りに繋がる何か仕様を変えるときにも、機械では難しくても人はすぐに対応できますから。
ただね、頭を護ると言っても限界があるんです。ヘルメットの内部になるべく衝撃のエネルギーを入れないようにして、できるだけヘルメット自体を使わないようにしたい。それを私たちは『かわす性能』と言います。その性能が形状で変わってくるんです。そして実際にヘルメットを使わなくてはいけない時に大切なのがシェルの剛さ。そのシェルの製造工程を今日は見ていただきます」と原田さんに案内されながら、この日の工場見学は始まった。
そして秘密裏な工場に潜入して驚いた。そこには、これまで知る由もなかったアライヘルメットのモノづくりの世界が広がっていた。職人集団だか、その全員が技術だけでなく優しさや気遣い、向上心を持ってモノづくりに挑んでいたのだ。そこにはまさにヘルメット屋のプライドがあった。
ノーマルのグラスファイバーは曲げると簡単に折れてしまった(左)。しかし、アライヘルメットに使われているスーパーファイバーベルトは折り曲げるのも難しく、しなって粘って、何度折り曲げてもなかなかちぎれない(右)。
アライヘルメットは欲しい素材、必要な素材を自らつくっていく。スーパーファイバーは工場内にあるシートベルトをつくる機械で製作。ファイバーの組み合わせで、様々な特性を出すことが可能だ。
人の「目」と「手」に委ねられている、アライヘルメットのモノづくり
最初に見せてもらったのは、ヘルメットのベースともいえる仮成形品(プリフォーム)の製作現場。
仮成形品は、ヘルメットのベースとなるもの。ガラス繊維で成形していくのだが、束になっている繊維をほぐして、数センチにカットしてノリを出しながら回転している型に飛ばして成形していく。
アライヘルメットが使用するガラス繊維は、髪の毛よりもはるかに細い数ミクロン。圧倒的に細い繊維が束ねられ、それを使うことで強い帽体を実現している。コストは嵩むが妥協せずに理想の素材を追求し続けている。
成形するといっても出来上がってきた物はとても軽く、繊細で、フワフワ。少しでも強く触ったら簡単に形を崩してしまいそうなイメージだ。強度を上げようとしてノリを増やしたりすると硬くなり、この後の工程で使えないのだという。
ガラス繊維1本の太さは数ミクロン。繊維メーカーとどんな繊維がヘルメットに合うかを協議しながらアライヘルメットに適した数値に辿り着いた。細いと繊維同士の接着面積が増え、繊維同士を抱き合わせるほど強くできるのは想像に難しくない。
繊維を型に吹き付ける機械は、毎回同じところからスタートするギヤ式。昔はタイヤで回していたため、スリップなどして同じ場所からスタートできなかったが、これも機械を作るメーカーと共同で開発した。
それでも一部が薄くなってしまったりすることがあり、そういった物は1回ノリが付いてしまっているため妥協無く廃棄となる。
出来上がった仮成形品を掲げ、職人の目が光る。均一に繊維がついているか目視で入念にチェックをして重さを計測。ヘルメットの種類によって仮成型品に細かく重量が指定されている。ヘルメットにはこれが2つ必要になる。もちろん各ヘルメットの規定の重量に収まっていなければそれも廃棄となる。
仮成形品は、アライヘルメット専用の機械をフル稼働させると1日に1000個分近くをつくることが可能。ヘルメットの種類はもちろん世界各国に合わせつくり分ける。仮成形品は優しく触らないと崩れてしまいそうなほど繊細だ。
季節や温度でセッティングを変えていく
最初の工程とそこで出来上がってくる物はとても繊細で、ヘルメットの原型といわれないとわからないほど。とはいえ、重さに関してはこの初期段階からかなりシビアである。製作しているスタッフからは、なんとも言えない緊張感が漂う。
「働くスタッフは、頭を護るということに誇りを持てる人でないといけないんです。だからご自身でバイクに乗っている方、ご家族で誰かがバイクに乗っている方、ヘルメットを被る人が他人とは思えない人を採用することを心がけています。
自分を護る、家族を護る、ライダーやレースでヘルメットを被る人達を護る。そんな気持ちのスタッフがアライでは、多いですね」とアライヘルメット取締役副社長の新井章仁さん。
次の工程では仮成形品にスーパーファイバーを貼る作業。穴を開ける場所はもちろん、強くしたいあらゆる部分に最適な素材を貼っていく。おでこの部分などは仕上がり状態を良くするため、薄い柔らかい生地で表面をカバー。
ヘルメットの種類やサイズ、そして販売する国によって異なる生地を使うからそのバリエーションは果てしない。もちろんこの工程はすべて手作業だ。
驚いたのは、仮成形品をつくるスタッフと生地を貼るスタッフが話をして『今日の帽体』を考えるのだという。今日の気温、湿度、毎日手で触って目で見ているからこそ分かる違いがそこにはある。
日々、人々がセッティングをしながら製品を仕上げているのである。
知られざるアライヘルメットの中身 Vol.2【とにかく重さにシビア。帽体の中に入れる本体の生地は3g以内の精度で製作】に続く。
アライヘルメット執行役員常務の原田重行さん(左)と、取締役副社長の新井章仁さん。この日は小雨がぱらつく天気だったが、大宮にある本社から群馬の榛東工場までバイクで移動。「ヘルメット屋なんだからヘルメット被るのは当たり前」と原田さん。
※本記事はアライヘルメットが提供したもので、一部プロモーション要素を含みます。※掲載内容は公開日時点のものであり、将来にわたってその真正性を保証するものでないこと、公開後の時間経過等に伴って内容に不備が生じる可能性があることをご了承ください。※特別な表記がないかぎり、価格情報は税込です。