【感動創造工場“ヤマハの手”Vol.6[最終回]】最高峰は、実はヤマハのスタンダード!? YZF-R1のエンジン組立技術
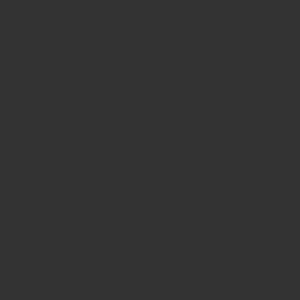
![【感動創造工場“ヤマハの手”Vol.6[最終回]】最高峰は、実はヤマハのスタンダード!? YZF-R1のエンジン組立技術](https://young-machine.com/main/wp-content/themes/the-thor/img/dummy.gif)
世界広しと言えども、ヤマハ発動機ほど作り手が“アツい”2輪メーカーもないだろう。細部まで徹底的に作り込まれ、こだわりを尋ねようものなら技術者の話はとどまることを知らない。そのすべては“ユーザーに感動を与える最高の製品を”というヤマハの企業理念「感動創造」に起因するものだ。その感動を工場から送り出す製造技術者の奮闘に迫る短期集中連載、最終回はヤマハのフラッグシップ・YZF-R1を取り上げる。
●文:大屋雄一 ●写真:山内潤也/ヤマハ発動機/YM archives ●BRAND POST提供:ヤマハ発動機
ヤマハの最先端技術の結晶、それがYZF-R1だ
今からちょうど10年前の2014年11月。イタリアはミラノで開催されたEICMAにおいて、7代目となるヤマハのフラッグシップ“YZF-R1”が華々しくデビューした。プレスカンファレンスのステージに乗車して登場したのは、かのバレンティーノ・ロッシだった。
「限界が近づくと、彼女(=YZF-R1)は『もっと速く走れるよ』ってささやいてくるんだ!」2014年のEICMAでそう語ったバレンティーノ・ロッシ。当時のPVではSUGOを走らせている。
1998年に誕生し、その時代におけるヤマハの最先端技術の結晶として成長してきたYZF-R1。初代から数えて7代目となる2015年モデルは、モトGPマシンYZR-M1の技術思想を体感できる、サーキット最速のポテンシャルを備えたモデルとして登場した。新設計の998cc水冷4ストローク並列4気筒エンジンは、先代からおよそ18psもパワーアップし、歴代初となる200psもの最高出力を達成した。
2015モデルとして登場した7代目YZF-R1。1998年の初代以来、公道も視野に置くスーパースポーツとして進化してきたが、この代でガラリとコンセプトチェンジ。最先端の電子制御を満載したサーキットウエポンに生まれ変わった。
排ガス規制対応など2022年の改良を経て、今秋に登場した2025年型YZF-R1(海外向けモデル)。カーボン製ウイングレットやKYB製の新型Fフォーク、ブレンボ製キャリパーなどを新装備した(YZF-R1Mはウイングのみ装着)。
2015年以降のYZF-R1の戦績を振り返ると、2021年にスーパーバイク世界選手権でタイトルを獲得したのをはじめ(ライダーはトプラク・ラズガットリオグル)、鈴鹿8耐では2015年から2018年まで4年連続で総合優勝。さらに国内のJSB1000クラスでは、2017年を除き9度の年間王者に輝いている。まさに歴史を築いた傑作といっても過言ではないだろう。
高回転化&軽量化のために専用部品を惜しみなく投入
【藤倉恭平さん(第2PT設計部 MC-PT設計4G CP4系/R25系 EG設計プロジェクトチーフ)】 2009年入社。MT-07/09/10など、大型スポーツ系のヘッド・動弁系設計を担当。その後は小型スクーターの駆動系設計などを経て、2023年からはCP4系/R25系エンジンのまとめ役。
そんな世界最強クラスのYZF-R1。現在そのエンジン設計を担当する藤倉恭平さんは、開発当時の様子を次のように振り返る。
「2015年型のYZF-R1は、サーキットで競り勝つことをテーマにしたモデルですので、徹底した軽量化が目標とされました。それを達成するために、車体ではマグネシウム鋳造ホイールやアルミ製燃料タンクなどを採用しています。
エンジンについては、最高出力の発生回転数を先代比で1000rpm引き上げる(1万2500→1万3500rpm)ことが目標とされましたので、フィンガーフォロワー式のロッカーアームやFSチタンコンロッド、鍛造ピストン、フリクションロスの低いピストンリングなどを導入しました。」
「そして、エンジン本体も軽量化の対象でしたので、クラッチカバーやACMカバーなどを固定するM6ボルトは、スチールからアルミへと変更しています。」
ボルトを一般的なスチールから軽量なアルミへ。カスタムシーンではしばしば用いられる手法だが、その材料置換は一筋縄ではいかない。使われているのはACMカバー、クラッチカバー、カムチェーンカバー、そしてブリーザーカバーの4か所で、締結する順序はもちろん、その締め方にも厳格なルールが定められている。
左右エンジンカバーなどのボルトは7代目YZF-R1専用のアルミ製。ちなみに同系エンジンのMT-10は鉄製ボルトで、同位置で比較すると、YZF-R1用アルミ製=750円/本、MT-10用鉄製=95円/本(ともに価格は税抜)と、パーツ価格は文字通りケタ違い。しかも再利用はNGだ。
具体的には、まず締結順序に従って6Nmのトルクでボルトを一度締め(スナッグトルク、捨て締めとも呼ばれる)、次に1本ずつ緩めてから、今度は3Nmで締めたあとに角度締めを行う。これは角度法と呼ばれ、ボルトの軸力安定化に効果的な手法だ。シリンダーヘッドやクランクケースの合わせなど重要な箇所に用いられるが、カバー類ではとても珍しい。
そして、この場所に採用されたアルミボルトは塑性変形して軸力を出す設計とされており、緩めても弾性変形のように元の形状には戻らないため再使用は不可となる。これはYZF-R1のサービスマニュアルにも厳しく記載されている。
ボルトと言えば、カムホルダー(ヤマハではカムキャップと呼称。カムブラケットとも呼ばれる)を固定するボルトにも軽量化の波が及ぶ。位置決めのためのノックピンが入る場所には首下40mmのボルトを、そうでないところには35mmのボルトを使用し、5mm分の軽量化を実施している。
組み立てる側としては、すべてのボルトの長さが同じであれば間違えようがない。しかし、YZF-R1の場合はたった5mm違いの長さのボルトを正確に組み付ける必要がある。このとてもハードルの高い組立作業をミスなく行うために、わざわざボルトの色を変えているのだ。
わずか5mmのボルト長短縮にもこだわる。40mmボルトは黒、35mmボルトをシルバーとして差別化はするが(右写真参照)、組立作業は間違いなく煩雑化する。それでも軽量化を優先するのがYZF-R1だ。
FSチタンコンロッドを採用するのはYZF-R1だけで、同系のCP4エンジンを搭載するネイキッドのMT-10、および北米向けのYZF-R1Sはスチール製となる。チタンコンロッドのボルトは、正確に軸力を管理するために油分の付着はNGだ。
一方、メタル部分には油圧がかかるまでの初期潤滑としてオイルを塗布する必要がある。こんなに接近した箇所で油分の要不要が求められるパーツはとても珍しく、チタンコンロッドを採用する上での組み立て上の難しさがここにある。
エンジンの高回転化に貢献するチタンコンロッドだが、組み立て時の油分管理には細心の注意が必要。高価なため、そもそも採用自体のハードルが高いパーツだが、それは組み立ても同様なのだ。
組み立てからは逸れるものの、YZF-R1のコンロッドは“かち割り”と通称されるFS(Fracture-Sprit=破断分割)式。大端部を文字通り割ることで本体とコンロッドキャップの締結強度を高める方法で、見ての通り、組み付けると断面が分からなくなるほど密着度が高い。
また細かい部分では、シリンダーヘッドの鋳造後に中子の砂を抜くための穴を埋めるM18の砂抜き穴埋め栓は、MT-10がスチール製なのに対し、YZF-R1にはアルミ製が用いられる。さらに、動弁系に使われるシム(ヤマハではパッドと呼称)に至っては、DLCコーティングされたロッカーアームとのフリクションロスを極限まで減らすため、YZF-R1専用に摺動面を超仕上げしたものを新作しているのだ。
その他、鍛造ピストンに組み込まれるピストンピンクリップは、ヤマハ内で最大線径のものを使用していたり、ピストンリングはヤマハ内で最薄レベルのものを用いるなど、そのこだわりは細部にまで及んでいる。そうした大小さまざまな積み重ねによってYZF-R1史上最強となる200psを達成しており、数々の輝かしい戦績にも結び付いているのだ。
ここも本文の内容からは逸れるが、YZF-R1は4気筒すべての燃焼室を機械加工し、容積を極限まで均一化している。メーカー製チューニングエンジンとしても過言ではない。
ハードルの高いYZF-R1のエンジン組立、それはPW50とともに
ヤマハの最先端技術の結晶であるYZF-R1は、すべて静岡県磐田市にあるヤマハ発動機の本社工場で産声を上げ、そして世界中へと旅立っている。完成車がアセンブルされるのは7号館であり、エンジンはその隣にある5号館で組み立てられている。
生産本部・製造統括部の尾関 渉さんが、この5号館の概要を説明してくれた。
【尾関 渉さん(組立工場推進課 総務チーム】2012年入社。IM事業部(現ロボティクス)で電動車いすの設計を中心に、商品企画、評価解析、生産準備、品質管理、サービス、規格認証などを担当。2023年より現在の部署に異動し、工場環境整備や工場見学などを担当する。
ヤマハの最先端技術の結晶であるYZF-R1は、すべて静岡県磐田市にあるヤマハ発動機の本社工場で産声を上げ、そして世界中へと旅立っている。完成車がアセンブルされるのは7号館であり、エンジンはその隣にある5号館で組み立てられている。
「5号館ではさまざまな機種のエンジンを組み立てています。小さなものは空冷2スト単気筒のPW50、大きなものは水冷並列4気筒のFJR1300ですね。その他にXV950やXV250といった空冷Vツインもあります。こうした排気量や気筒数の異なるエンジンを、すべてAとBという2つのラインで組み立てているんです」
本社工場5号館の見取り図。左上の車種リストのとおり、単〜4気筒、空冷に水冷、並列にV型、2ストに4スト…と、ありとあらゆる形式のエンジンを2つのラインで組み立てている。
YZF-R1のエンジンは見取り図右側のAラインで組み立てられる。構造が複雑で組み立てに細心の注意が必要なYZF-R1のエンジンも、他車と共通のこのラインで組み立てるのが前提。それはすべてのエンジンを同じクオリティで組むことにも繋がる。
先に説明したとおり、ボルトの長さや材質、シムの仕上げまで専用品としたYZF-R1のCP4エンジンも、じつはこの5号館のラインで組み立てられている。読者の中には「ひとりの匠が1基ずつ、クリーンルームで丹精込めて組んでいる」とイメージしていた方がいるかもしれない。しかし、ヤマハはコスト増になるであろうそうした手段をあえて選択せず、製造ラインの作り込みを行うことで、すべてのモデルを同じ品質で組み立てることに注力しているのだ
「当然ながらYZF-R1とPW50とでは、要求される設計上のハードルの高さも部品点数も異なります。そうしたさまざまなエンジンを同じラインで組み立てるために、こだわっているポイントがいくつかあります」
【深尾健治さん(組立技術部 EG組立技術G)】 2019年入社。MT-07の完成車生産準備を担当後、2020年からはエンジン生産準備担当として、YZ250/450、WR250/450、MT-07/09などのエンジン生産準備に携わる。
と、説明してくれたのは、生産本部・製造技術統括部の深尾健治さんだ。
5号館での組立ラインの流れを簡単に紹介しよう。まずは上下が分離された状態のクランクケースに打刻を行ったあと、ベアリングやオイルシールを組み付ける。次にトランスミッションなどを組み込み、クランクケースの上下を合わせる。その後、左右からACG(オルタネーター、ヤマハではACMと呼称)やクラッチなどを組み込み、ボディシリンダー、シリンダーヘッドの順で組み上げたら、エンジンの形としては完成となる。
最後は匠によるリーク検査や外観チェックなどが行われ、すべてクリアしたものだけがストックヤードを経て、完成車が組み立てられる隣の7号館へと送られる仕組みだ。
腰下から上へ進み、検査を経て完了
ラインでのエンジン組み立てはクランクケース(腰下)からスタート。YZF-R1の場合、細かなパーツを組み付けた後、アッパークランクケースにシリンダーを装着し、コンロッドが組まれたピストンを挿入(左写真)。その後、ケースをひっくり返してクランクシャフトやトランスミッションを載せていく(同右写真)。
そしてコンロッドをクランクシャフトと合体させ、コンロッドボルトを締め上げていく。ここはエンジン内でもとくに重要なボルトで、締め付けトルクやその角度は電動ツールで厳密に管理される。この後、バランサーシャフトなどを組み込んでロアークランクケースを被せる。
シリンダーヘッドはバルブやカムシャフトを組んだ状態でライン脇に一時ストックされ、エンジンに載せてカムホルダー締め付けやカムチェーンの装着などを行う。その後はクラッチ周辺パーツなどを組み込み、カバー類のアルミボルト締め付けへと進む(この様子は後述)。
エンジンスタッカーへの搬入/搬出は完全自動
完成したエンジンが一時保管される「エンジンスタッカー」。Bラインの脇にあり、組み立てを終えたエンジンがAGV(無人搬送車)で次々と運び込まれる。
そして、同じく本社工場の7号館で行われる車両の組み立てに合わせてエンジンが搬出されていく。このスタッカーからの搬出も完全自動。無人走行車がエンジンを載せた台車を牽引していく。
他モデルと工数を揃えるためにR1専用ツールを開発
YZF-R1のCP4エンジンでは、先ほども説明したとおり、カバー類にアルミボルトが使われている。一般的なスチール製のボルトに対して1本あたり2.7〜5.1gの軽量化が図れる上に、クランクケースと同じ材質のため、熱膨張による緩みが発生しにくいというメリットがある。
反面、軸力を限界まで引き出すために角度法が必要な設計とされているため、スチールボルトのトルク法よりも工数が増えてしまう。つまり、YZF-R1のエンジンだけ組み立てに時間がかかってしまうのだ。
この課題をクリアするために、深尾さんは電動ツールの改良を実施。締め付け時間を短縮するために回転速度を上げ、さらに作業者による手元の角度のばらつきを低減する締め付け方法を編み出したのだ。
こうした角度法はクランクケースなどにも用いられており、そちらでは専用のストッパーをはめ込んで正確に締め付けツールの角度を管理している。YZF-R1における電動ツールの改良は、こうした治具を使わないのでそれを脱着する時間が不要であり、さらに作業者ごとのクセも吸収できるという素晴らしいものだ。
実際の組立ラインでは、そうした工夫の甲斐もあって、作業者はリズム良く電動ツールでカバー類のアルミボルトをチュイン、チュインと締め付けている。本来なら捨て締めしたあとに一度緩め、本締め後に角度締めを行うのだから、このスピードアップの恩恵は想像にがたくない。
エンジンの左右、3枚のカバー類だけで計23本のアルミボルトが使用される。本来なら素材の物性の違いにより、その締め付けには鉄ボルトより多くの手間と時間が必要となる。
しかし、電動ツールの改良などによりそれを克服。組み立て作業者は通常の鉄製と変わらぬ様子でアルミボルトを締め付けていく。グラム単位のわずかな軽量化ですら、数多くの工夫に下支えされているのが分かる好例だ。
同様の工夫は、ピストンピンクリップの組み付けにも及んでいると教えてくれたのは、深尾さんと同じグループに属する清水凌雅さんだ。
【清水凌雅さん(組立技術部 EG組立技術G)】 2022年入社。生産ラインの立ち上げや移管を担当しており、入社直後はエンジンAラインの移管と、同ラインにPW50を移管する業務を担当。2023年からはエンジンBラインの立ち上げにも関わる。
「YZF-R1の高回転に耐えるため、線径が太くて線長の長いピストンピンクリップを採用しているのですが、硬すぎて通常のサークリッププライヤーでは歯が立ちません。そこで、専用工具を開発しました」
YZF-R1に使われているピストンピンクリップは、通常のφ1.2mmに対してφ1.6mmと太い。しかも線長が長いため、そのはめにくさは相当なものだ。これを組み付けるために開発された特殊ツールは先端がテーパー状になっており、クリップの1か所を溝にはめてからスライドさせると全周が簡単に収まる仕組みだ。そして、きちんと溝の全周にはまっているか、クリップが塑性変形していないかを確認するための治具も専用で作っており、作業者がすぐに確認できるという工夫も盛り込まれる。
YZF-R1専用のピストンピンクリップ装着ツール。これもアルミボルトによる軽量化と同様。極限の性能を追求するという華やかな行為は、表に出ることの少ない、言ってしまえば地道な作業や創意工夫の積み重ねが支えている。
その他、薄肉ピストンリングをボアピッチの狭いシリンダーに組み込むため、YZF-R1専用にピストンサブ組みツールが作られた。作業者の手元を見ていると、先ほどのアルミボルトの組み付けと同様に、作業者はピストンをスッ、スッとシリンダーに滑り込ませているので、薄肉ピストンリングによる外れやすさなどは微塵も感じない。
こうした数々の専用ツールの開発も、製造ラインの作り込みの一環であり、他モデルと同等の工数で組み立てることが品質の安定にもつながるのだ。
今回の取材に対応してくださった、ヤマハ本社工場・5号館のみなさん。ここで組み上げられたエンジンは7号館へと運ばれ、車両としてアセンブルされていく。
【取材後記】YZF-R1もYZ系もPW50も、同じラインで組むことの難しさ
今回の取材では、バッテリーを動力にスターターモーターを回し、クランクシャフトを回転させられるカットモデル(写真中央)も見物させてくれた。ギヤチェンジも可能という凝ったもの!
国内有数のアルミ鋳造メーカーとしての顔も持つヤマハ。エンジンで言えばシリンダーやシリンダーヘッド、クランクケースがそれに該当し、美しく、そして精密に加工される。その他、じつはカムシャフトやコンロッド、クランクシャフト、トランスミッションといった主要パーツも内製しており、それらが最終的に運ばれてくるのがエンジン組立ラインのある5号館なのだ。
ここは鋳造工場のように火力を使うわけでも、また大きな騒音や切粉を発生する加工機械があるわけでもないので、他と比べるととても快適な環境だ。空調も行き届いており、5号館全体がまるでクリーンルームのようだ。
そんな過ごしやすい工場内で、ヤマハ車のエンジンはていねいに組み立てられている。YZF-R1というヤマハの精神的支柱とも言えるエンジンを組んでいるからこそ、品質も底上げされている印象だ。
どの作業者も慣れた手つきでパーツを組み込んでいるが、それは専用ツールや治具の開発といった、生産本部のメンバーの努力があればこそ。フラッグシップが別の機種になったとしても、この伝統は永く受け継がれるだろう。
※本記事はヤマハ発動機が提供したもので、一部プロモーション要素を含みます。※掲載内容は公開日時点のものであり、将来にわたってその真正性を保証するものでないこと、公開後の時間経過等に伴って内容に不備が生じる可能性があることをご了承ください。※特別な表記がないかぎり、価格情報は税込です。