【感動創造工場“ヤマハの手”Vol.5】688ccパラツイン“CP2” 熟成の名機の陰に、生産体制の技術革新あり
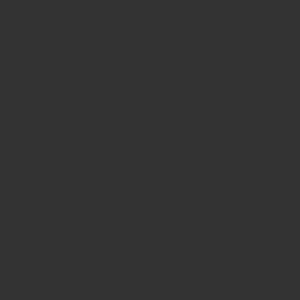
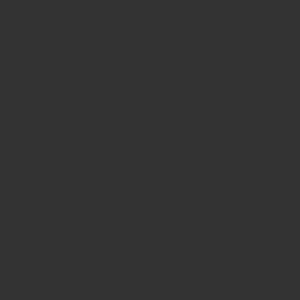
世界広しと言えども、ヤマハ発動機ほど作り手が“アツい”2輪メーカーもないだろう。細部まで徹底的に作り込まれ、こだわりを訪ねようものなら技術者の話はとどまることを知らない。そのすべては“ユーザーに感動を与える最高の製品を”というヤマハの企業理念「感動創造」に起因するものだ。その感動を工場から送り出す製造技術者の奮闘に迫る短期集中連載、第5回はMT-07などに搭載される並列2気筒エンジンにスポットを当てる。
●文:大屋雄一 ●写真:山内潤也/ヤマハ発動機/YM archives ●BRAND POST提供:ヤマハ発動機
誕生から10年、さまざまなカテゴリーで活躍するCP2
■ヤマハCP2エンジン
MT-09から遅れること4か月。2014年8月20日に発売されたMT-07の衝撃は、10年が経過した今も忘れられない。新開発の688cc水冷パラツインは極低回転域から粘り強く、4000rpmから8000rpmにかけて気持ち良くトルクが上乗せされていき、そしてレッドゾーンの始まる1万rpmまできっちりと吹け上がる。回転域ごとの表情の変化が豊かであり、スロットルを大きく開ければ軽い車体と相まって脱兎のごとく加速する。
この水冷並列2気筒エンジンは、270度位相クランクを採用する。今でこそパラツインにおけるベーシックなエンジン形式の一つとなっているが、先鞭をつけたのは何を隠そうヤマハだ。1995年3月に発売されたTRX850が世界初であり、MT-07のエンジンはそのDNAを正しく受け継いでいる。
先にMT-09が水冷トリプルというキャッチーなワードで誕生したこと、また最高出力73.4psをはじめスペックに華々しさがないことなどから、やや控えめなデビューであったことは否めない。
しかし、69万4000円(当時)という戦略的価格が業界に与えたインパクトは強烈で、発売翌年の2015年には401cc以上の販売台数ランキングにおいて堂々のトップとなったのだ。付け加えると第2位はMT-09であり、この年はヤマハが1-2を飾っている。
このパワーユニットは、クロスプレーン・2気筒の頭文字から“CP2”エンジンと名付けられ、後にスポーツヘリテイジのXSR700、アドベンチャーモデルのテネレ700、スーパースポーツのYZF-R7、そしてスポーツツアラーのトレーサー7(日本未発売)と、さまざまなカテゴリーのバイクに搭載されていく。この汎用性の高さは驚きに値しよう。
今回の“ヤマハの手”では、そんな名機CP2エンジンのモノづくりの秘密に迫りたい。
(左上から時計回りに)XSR700/テネレ700(2025モデル)/トレーサー7/YZF-R7。どんな車両に搭載されても好マッチングを見せるのは、CP2エンジンに備わる高い汎用性にほかならない。
今秋に発表されたばかりの最新型MT-07。CP2エンジンはついに電子制御スロットルを獲得し、MT/ATを切り替え可能なY-AMT仕様も登場するなど、着実に進化を続けている。
設計側と製造技術側が密に連携して開発
【川端哲也さん(PTユニット プロダクト開発統括部 第2PT設計部MC-PT設計2G)】 主に大型モデルの駆動系やシリンダーヘッド、動弁系の設計を担当。2022年からはCP2のプロジェクトチーフとして設計を取りまとめる。
「CP2エンジンは、現在5機種に搭載しています。スーパースポーツからアドベンチャーまでカテゴリーはさまざまですが、どのモデルも完成度が高く、このエンジンの汎用性を象徴していると思います」
CP2エンジンの開発に携わったMC-PT設計グループの川端哲也さんは胸を張る。
一般的に二輪車のエンジンに求められるのは、パワーなどの純粋な動力性能をはじめ、信頼性や燃費/規制、軽量/コンパクトといった基本機能があり、さらにプラスアルファの要素としてデザイン性や静粛性といった魅力機能が挙げられる。CP2エンジンは、部品点数の少なさや前後長の短さに注力しており、具体的にはバランサーを1軸(TRX850は2軸だった)としたり、ウォーターポンプとオイルポンプを同軸にするなどして、信頼性や軽量/コンパクトを追求している。
加えて他のエンジンではあまり見られないのが、始動時の圧縮を減らすデコンプ機能だ。これによってスターターモーターやバッテリーの小型化が可能となり、軽量/コンパクトに貢献するだけでなく、ひいてはコストダウンにもつながっているのだ。
ちなみに、ドイツの二輪専門誌「モトラッド」の名物企画である5万km耐久テストにおいて、2022年度はCP2エンジンを搭載するMT-07が1位、テネレ700が2位となるなど、高い信頼性が証明されている。
このCP2に限らずヤマハ車のエンジンは、主要パーツを自社工場で内製している。いくら設計が優れていても、それを限りなく正確に製造する技術がなければ、狙った性能は発揮できない。ヤマハは内製だからこそ、設計側と製造技術側が密に連携することができ、お互いが高め合い支え合って、よりよいモノづくりを実現しているのだ。
ケースはダイキャスト、ヘッドはLP鋳造
それでは、CP2エンジンの主要パーツの中から、クランクケースとシリンダーヘッドの役割と、それらを設計することの難しさについて説明しよう。
まずはクランクケースから。これは薄肉成型が可能なアルミダイキャストで作られている。主な役割は、クランクシャフトやバランサーシャフト、トランスミッションといったムービングパーツの支持であり、さらにCP2エンジンの場合は部品点数削減のために、アッパークランクケースがシリンダーと一体となっているほか、後方にはリヤショックユニットのマウントが設けられている。
数多くの役割が求められるクランクケース。各シャフトの支持はもちろんだが、ダイヤモンドフレームのCP2では車体の剛性メンバーでもあり、かつサスペンションからの入力も受ける。軽量化や製造性なども考慮し、肉厚は極力薄くしつつ軸受けには梁を立てるなど、最小限の肉付けで剛性を確保している。
加工時に各シャフトの軸間距離がわずかでもずれれば、ギヤのバックラッシュが拡大して異音が発生し、また軸穴の精度に問題があれば、ギヤが偏当たりしたり、パーツ同士が干渉したりする。その他、オイル通路を設けるための複雑な加工や鋳巣対策が必要など、パーツとしては上下二つなのに、求められる設計要件は山ほどある。ゆえに、製造技術側との連携が重要なのだ。
【徳永駿さん(PTアルミ技術部鋳造技術4G】入社以来、一貫して鋳造技術に関与。現在は低圧鋳造の工程設計・生産準備で、主にシリンダーヘッドを担当する。
続いてはシリンダーヘッドだ。ヤマハではヘッドシリンダーと呼ばれている。PTアルミ技術部鋳造技術第4グループに所属し、低圧鋳造の工程設計や生産準備を担当している徳永駿さんが説明してくれた。
「アルミ鋳造には、溶湯を流し込む重力鋳造、じっくりと押し込む低圧鋳造(ロープレッシャー=LP鋳造)、そして瞬間的に打ち込む高圧鋳造(ダイキャスト)の3つがあります。シリンダーヘッドは、中子による中空構造の成型が可能な低圧鋳造で作っています」
CP2エンジンのシリンダーヘッド(写真は試作サンプル)。水冷DOHC4バルブ、サイドカムチェーンとスペック的には一般的なものだが、設計や製造にはヤマハ独自のノウハウが数多く注がれている。
これもクランクケースと同等以上に複雑かつ機能要求が多い。一般的に燃焼ガスの温度は1000℃と言われており、排気ポートを開閉する排気バルブは700℃近くに達する。耐熱鋼で作られた排気バルブの軸が最大で1mmも熱膨張すると聞けば、その過酷さが想像できるだろう。
さらに、燃焼室は最大で4トンもの燃焼圧による荷重を受ける。4トンと言えばアジアゾウ1頭分の重さだ。MT-07の最大トルク発生回転数は6500rpmなので、1秒間に約54回もこの燃焼圧を受けていることになる。そして、それだけ激しい力を受け続ける燃焼室の上方では、カムシャフトをはじめとする動弁系の正確性が求められるのだ。
シリンダーヘッドに求められる機能の一覧。燃焼圧はヘッドを逆Uの字に曲げるような入力を加えるため、剛性が低いと動弁系の作動に影響する。また、吸排気ポートは鋳造時に中子で成形されるが、ここが1mmズレるだけで流量に影響が出る。設計/製造ともに難易度の高いパーツなのだ。
エンジンの中で最も高温になる排気バルブ周辺を冷やさなければ、バルブシートが摩耗しやすくなる。よって2本ある排気バルブの間にも冷却水を通したい。そうした設計側の切なる願いに対し、鋳造担当は、砂で作られる中子は崩れやすく、もし崩れたら不良を発見しにくいであろうと悩む。さらに加工担当は、プラグホールに必ず設ける水抜き穴を振れが出ないように開ける手段を検討する。こうして各パートが知恵を出し合った結果、CP2エンジンは世界でもトップクラスの信頼性を勝ち得たのだ。
医療用のCT検査装置で設計要件を満たしているか判断
【井口勇哉さん(磐田第3製造部品質改革課 品質管理)】2輪エンジン/マリンエンジン/自動車用エンジン部品など、アルミ鋳造部品全般において主に寸法の品質保証を担当。
国内有数の鋳造メーカーとしての顔も持つヤマハ。創業以前からのピアノフレームで培われた長年の鋳造技術があるだけに、そのノウハウは膨大であり、他社からの信頼も厚い。そして、製品の解析技術でも大きくリードしている。
「現在は医療用のCT検査装置を用いて、鋳巣やクラックなどの内部欠陥を把握しています」
そう教えてくれたのは、磐田第3製造部の井口勇哉さんだ。
CTスキャンはコンピュータ断層撮影とも呼ばれ、放射線などを利用して物体を走査し、データを処理することで物体の内部構造を画像として構成するものだ。人間ドックなどで体験したという方もいるだろう。ヤマハで使われているのはまさに医療用であり、アルミパーツ向けにチューニングしたものだ。量産前の生産準備の段階で鋳物の弱点部位を割り出し、内部欠陥が出ないように鋳造条件を修正。量産体制に入ってからは、先に特定された弱点部位を抜き取り検査し、不良品の発生を未然に防ぐ体制を整えている。
そして、現在はディープラーニング型のAIが導入されており、弱点部位の自動判定が行われているという。これによって高品質な製品をより安く、早く生産できるようになったのだ。
かつては実際にパーツを輪切りにし、職人の手で行っていた検査を、CT検査装置の導入によって非破壊での内部品質確認が可能となり、さらに今ではその合否判定をAIができるようになったのだ。これは画期的な技術革新と言えるだろう。
中空部を作るための中子(なかご)にもノウハウが詰まる
そして、この解析技術の進歩は中子の測定にも及んでいる。
中空部のある鋳物を作る際には、中子と呼ばれる鋳型が用いられる。これに対して外形の鋳型は主型(おもがた)と呼ばれている。中子の原材料は、砂に熱硬化性樹脂をコーティングしたレジンコーテッドサンドで、作りたい形状の金型に充填して加熱すると中子が成型される仕組みだ。中子は鋳造後に回収されるので、これ自体がユーザーの手に渡ることはない。しかし、中子によって作られた鋳物の内面形状が性能を左右するので、これもまた大切な“パーツ”と言えるだろう。
燃焼室周辺の冷却水路と、吸/排気ポートを成形する中子。これらをシリンダーヘッドを鋳造する金型の中に配置し、溶湯(溶けたアルミ)を流し込むと中子の部分が空洞で成形される。
今回の題材であるCP2をはじめ、昨今のエンジンは高効率化やコンパクト化、軽量化を推し進めたことにより、シリンダーヘッドの形状が複雑化の一途を辿っている。以前は接触型三次元測定器を用い、プローブ(触針)を測定対象である鋳物に接触させて検査を行っていた。しかし、外側から測定できる範囲には限りがあるため、内部寸法の保証は切断による肉厚測定のみとなっていたのだ。
現在は、先に紹介したCT検査装置に加え、中空部の基となる中子の形状を精密に測定することで、内部寸法の保証を行っているという。
レジンコーテッドサンド。触った感じはサラサラした普通の砂だ。
「中子も社内で作っているのですが、原材料となる砂を高圧で吹き付けて成型するので、何年も作っているとその中子型が痩せてきてしまいます。それを精密に測定し、適切な形状を維持管理することで、不良発生を未然に防ぐのが私たちの取り組みです(徳永さん)」
レジンコーテッドサンドは非常に粒子が細かく、グラニュー糖よりもはるかにサラサラとした感触だ。それを高圧で中子型に吹き付けるのだから、イメージとしてはサンドブラストに近いだろう。型が痩せれば中子はその分だけ大きくなり、例えばポート形状が変わってしまうと排ガスの数値にも影響が出るという。付け加えると、砂で作られる中子と金属製の主型とでは熱膨張率が異なるので、最終的な寸法を狙ってどのように型を設計するかは機種ごとに異なるとのこと。
この中子の測定は、MT-07が発売された2014年からスタートし、2016年にハンディータイプのスキャナーへ。2022年にはロボットによる自動化が行われ、そして現在はマーカーを使わない最新タイプへと進化している。エンジンのスペックには現れない部分だが、こうした地道な積み重ねが信頼性へとつながっているのだ。
より速く正確な測定値を求めスキャナーも進化。従来はハンディタイプをロボットアームに支持させて自動で行っていたが(左)、2023年からはマーカーレスタイプの最新マシン(右。写真では撮影用にシリンダーヘッドを測定中)を導入。“消える部品”である中子の形状保証のため、測定器も常にアップデートされている。
段取ロス“ゼロ”を達成した超汎用VIMライン
ダイキャストで作られたクランクケース、LP鋳造で作られたシリンダーヘッドは、切削加工工程へと歩を進める。メインで稼動しているのは、同一パーツを連続的に加工する旧来の専用加工ラインだが、2023年8月からはさまざまな機種のパーツを同時に加工可能なVIM(バリュー・イノベーション・マニュファクチャリング=価値を創造する)ラインが平行して稼動している。
このラインには8台のマシニングセンタがあり、機種やパーツごとに精密切削加工を自動的に行っている。パーツの移動はロボットとAGV(オート・ガイデッド・ビークル=無人搬送車)が行い、広大な面積にもかかわらず、オペレーターは人作業エリアに1名、そして完成検査を行う一人の匠という2名体制だ。
VIMは主に3つのエリアで構成される。図の加工エリア/AGVエリアは基本的に無人だ。
【藤井彰さん(PTアルミ技術部加工技術3G)】アルミ加工の工程設計・生産準備で、2輪エンジン/自動車エンジン/マリンエンジンなど様々な商材部品を担当。VIMラインではプロジェクトリーダーを務める。
PTアルミ技術部加工技術第3グループの藤井彰さんは、次のように語ってくれた。
「このVIMラインが生まれた背景には、高付加価値製品に絞った多品種少量生産というヤマハ本社工場ならではの体制にあるんですよ」
例えばYZF-R1のクランクケースの生産を終えたあと、CP2エンジンのシリンダーヘッドを加工する場合、刃物やプログラムの変更に加え、それらが変更した後の品質検査のために設備を停止する時間が必要となる。段取りロスと呼ばれており、これをゼロにする目的で誕生したのがVIMラインだ。狙いどおりタイムリーにお客様へ製品を届けられるようになり、まさに“価値を創造する”ラインと言えるだろう。
現在、このVIMラインではCP2エンジンのシリンダーヘッドをはじめ、FJR1300のクランクケースからAG200Fのシリンダーヘッドまで、全8モデルのパーツが切削加工されている。これらのパーツは機種の区別もヘッドやケースの区分もなく、完全に混在してライン上を流れている。
シリンダーヘッドについては、まずはマシニングセンタで各部の切削を行う。その後にバルブガイドとバルブシートを組み付け、この二つを同時に精密加工する特殊ツールで切削。さらに、バルブ当たり面とバルブガイドの振れについて抜き取り検査を行うという徹底ぶりだ。
1名のオペレーターは、クランクケースの上下を合わせたり、カムホルダー(ヤマハではカムキャップと呼称。カムブラケットとも呼ばれる)の組み付けといった、切削加工以外の作業に従事。これは機械よりも人の手による方が品質が高いとの判断からだ。そして、最終検査を行う匠は、外観のキズや出来映えなどを確認する。持続可能な社会を目指す上において、人が行うことの価値はどこにあるのかを追求した結果がここにある。
取材にご協力くださったヤマハ本社工場・12号館(エンジン部品加工職場)の皆さん。その中にあるVIMラインは色使いも鮮やかで、青いLEDでライトアップされた工程など、いい意味で工場らしくない雰囲気が印象的だった。
こうして“匠の手”を重視しているVIMだが、そこに投入されている自動化技術で注目したいのは「加工設備選択及び生産ルートの自動計算」という機能だ。これは鋳造を終えたエンジンの素形材をラインに投入すると、どの設備で加工し、どんな順番で次の設備に流すのか、そのルート設定を自動的に決定してくれるというもの。
もちろんライン内には今まさに生産されている部品や、そのために稼働中の工作機械がある。それらの混雑状況までも踏まえてベストなルートを算出するのだという。部品を淀みなく生産し、ユーザーにタイムリーに製品を届けるというVIMの狙いは、こうした最先端の自動化技術にも支えられているのだ。
なお、このVIMラインはGKデザイングループのひとつ、GK京都がカラーリングの検討やロゴデザインの作成に協力している。加工現場は切削油が飛び散ったり切り粉が発生するので、どうしても汚いというイメージを持たれやすい。それを払拭し、関わったメンバーのモチベーションアップや、見学者(家族)のヤマハに対するイメージをアップさせるのが狙いで、こうした取り組みも商品価値の向上につながるのは間違いない。
【取材後記】10年変わらないCP2、しかし生産体制は劇的に進化していた
ほぼ同時に発売されたMT-09のCP3エンジンは、2021年モデルで排気量をアップするなど大きく進化した。これに対してCP2エンジンは、YZF-R7がアシスト&スリッパークラッチを採用するなど小さな違いはあるものの、基本設計は10年前から変わっていない。
付け加えると、つい最近発表された2025年型のMT-07は、フレームや足まわりなどシャシーが飛躍的に進化したが、ことエンジンに関してはY-AMTをタイプ設定したり、ユーロ5+に適合するため吸気系を変更、電子制御スロットルの投入などが行われてはいるものの、エンジン本体に関してはほぼこれまでどおりとなっている。
裏を返せば、10年以上も活躍できるほど素性の良いエンジンということであり、これは大いに誇っていいだろう。一方で生産体制はこの10年で劇的に進化しており、これがさらに信頼性を高めているのは間違いない。今回の取材を通じ、名機“CP2”の設計および製造に携わっている皆さんの誇らしげな表情が印象的だった。
※本記事はヤマハ発動機が提供したもので、一部プロモーション要素を含みます。※掲載内容は公開日時点のものであり、将来にわたってその真正性を保証するものでないこと、公開後の時間経過等に伴って内容に不備が生じる可能性があることをご了承ください。※特別な表記がないかぎり、価格情報は税込です。