【感動創造工場“ヤマハの手”Vol.4】“YAMAHA SPINFORGED WHEEL”「パイオニアだから実現できた、次世代軽量ホイールの技術に迫る」
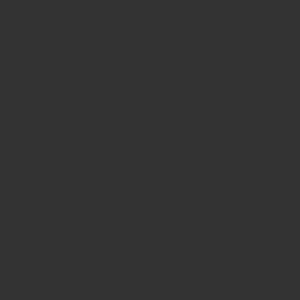
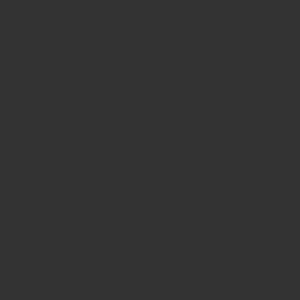
世界広しと言えども、ヤマハ発動機ほど作り手が“アツい”2輪メーカーもないだろう。細部まで徹底的に作り込まれ、こだわりを訪ねようものなら技術者の話はとどまることを知らない。そのすべては“ユーザーに感動を与える最高の製品を”というヤマハの企業理念「感動創造」に起因するものだ。その感動を工場から送り出し続ける製造技術者の奮闘に迫る短期集中連載、第4回は次世代の軽量ホイール“ヤマハ スピンフォージド ホイール”について。
●文:大屋雄一 ●写真:山内潤也/ヤマハ発動機/YM archives ●BRAND POST提供:ヤマハ発動機
1976年からアルミキャストホイールを内製するヤマハ
バイクに使われているパーツにおいて、路面と唯一接しているのはタイヤだ。そして、そのタイヤを介して車体を支えているのがホイールであり、つまりは人命をも支えている重要なコンポーネントと言っていい。
今でこそオンロードモデルはキャスト(鋳造)ホイール、オフロードモデルはワイヤースポークホイールという住み分けができているが、大昔はほぼすべてが後者だった。日本でキャストホイールが認可されたのは、今から46年前の1978年4月1日のこと。その認可の目安となる「二輪自動車軽合金ホイール技術基準(JWL)」の作成に積極的に参加していたのがヤマハなのだ。
JWLの試験項目には、回転曲げ疲労試験、半径方向負荷耐久試験、衝撃試験、ねじり試験などがあり、ヤマハでは独自にX線検査や染色浸透深傷検査なども追加。さらに、さまざまな強度テストや耐久テストも実施するなど、キャストホイールのパイオニアとして当時から果敢に業界をリードしていたのだ。
ちなみに、ヤマハ車で初めてキャストホイールを採用したのは、1976年10月に発売された海外向けのRD400だ。国内では1978年にリリースされたXS750スペシャル、GX400/GX250、RD50の4機種が最初であり、キャストホイール仕様は「SP」という名称でタイプ設定されていた。なお、当時からヤマハは自社でホイールを製造しており、これは二輪メーカーではかなり稀少な例である。
今回の取材に際してヤマハがまとめてくれた資料。キャストホイールの導入以降、エポックとなった機種はホイールにもなにかしらの話題が盛り込まれている。
ヤマハハンドリングの一翼を担うホイールの要件とは
そんな重要なコンポーネントのひとつであるホイールには、求められるおもな要件として次の3つが挙げられる。「強度」、「軽さ」、そして「デザイン」だ。機械好きなら、強度と軽さが相反することはなんとなくイメージできるだろう。そして、この2つの要素をうまくバランスさせた上で、さらにカッコいいデザインを盛り込むとなると、困難を極めるであろうことは想像にがたくないはずだ。
一体成型されるキャストホイールは、3つの部位で構成されている。タイヤが装着されるリム、中央にあるハブ、そして、この2つをつなぐスポークだ。リムについては、ホイールのもっとも外周にあるという位置的な関係から、この部位の重量が慣性モーメント、ひいてはハンドリングに大きく影響する。中央のハブは、ブレーキディスクやドリブンスプロケットが取り付けられるため、それを支えられるだけの強度を確保しつつ、ここもまたバネ下重量に影響するため軽いことが望ましい。そしてスポークについては、ホイールにおいてもっともデザイン性を左右する部位であり、加えて軽さも求められる。
そう、ホイールはすべての部位において軽いことが善とされているのだ。そして、操安性に大きく影響するホイールは、人機一体感が味わえる「ヤマハハンドリング」の一翼を担っているといっても過言ではない。
2輪用ホイールはおもに3つの部位に分類でき、それぞれ異なる役割を持つが、どのパートでも求められるのが“軽量化”だ。
ホイールで商品競争力を高めたいという思いが生んだ新製法
【香島 仁さん(機能モジュール開発部)】2000年入社。発電機のボディ設計やスクーターの車体設計担当を経て、2005年から現職であるキャストホイールの設計を担う。
そんな重要なコンポーネントのひとつであるキャストホイールを、1970年代から内製しているヤマハ。その設計や製造に携わっている社内のメンバーは、常に先を見据えた先行開発を行っている。
「ホイールは強度、軽さ、デザイン性といった相反する要素をうまくバランスさせなければならないのですが、設計側だけではもう軽量化の限界が見えてきて、2015年の12月末ごろにアイデアとして出たのが“回転塑性加工”だったのです」
そう話してくれたのは、スピンフォージドホイールの設計を担当した香島 仁さんだ。
回転塑性加工は“フローフォーミング”とも呼ばれており、4輪のホイールではメジャーな製法だ。鋳造後のホイール素材を回転させながら外周にローラーを押し当て、リム部を圧延して成型する加工で、強い圧力によって金属組織が密になり、強度が上がる分だけリム部の薄肉化、つまり軽量化が図れるというメリットがある。
フローフォーミング=回転塑性加工では、回転しているホイールのリム部にローラーを押し当て、素材を圧縮しながら薄く引き伸ばしていく。加工後の金属組織は図のようにギュッと密度が増している。
金属組織が鍛造製法並みに密になることから、ヤマハはこの製法で作られるホイールを“YAMAHA SPINFORGED WHEEL(ヤマハ スピンフォージド ホイール)”と名付けた。フォージドとは鍛造の意。名前に強度への思いを込めているのだ。
メリットしかないように思われるフローフォーミングだが、2輪用のホイールに採用されるのはこれが初となる。では、なぜこれまで採用されてこなかったのか。それは、外側しか見られない4輪用ホイールに対し、2輪用は左右両面が意匠となるため、フローフォーミングの回転台に固定するために必要な突起(デザイン的には不要なもの)の処理が困難だったからである。
3代目MT-09に間に合わせるための過密なスケジュール
【神田康成さん(生産本部 PTアルミ技術部)】2009年入社。カムシャフトの加工技術や生産準備(レクサスLFAにも関与)に関わった後、2019年に現部署である鋳造部門へ異動し3代目MT-09のフレームなどを担当。愛車はXS-1、DS6に最近増車したNMAX155。
フローフォーミングを採用することに目処が立ったのは、アイデア誕生からおよそ1年後の2017年1月のこと。ここまではあくまでも先行開発の領域だ。
ヤマハでは多くのコアコンポーネントを開発および内製しているが、実際に採用されるまでには多くのハードルを越えなければならない。それもまったく新しい技術となると、はたして量産できる代物なのかまで検証しなければならず、時間がいくらあっても足りないという。
「モノにできそうだと分かったのは2017年で、車両開発部隊がいろいろな評価をしている中、量産化開発も並行して進めました。評価が進むにつれ、3代目MT-09(2021年モデル)でスピンフォージドホイールを使ってもらえそうだということになり、生産ラインが稼働したのは2020年の8月のことですね」
そうやって当時を振り返るのは、アルミ技術部の神田康成さんだ。
繰り返しになるが、ホイールはハンドリングを左右するコアコンポーネントであり、モデル開発の初期段階でこれが決まっていないと、ジオメトリーもサスセッティングも決められない。つまり、スピンフォージドホイールの開発メンバーは、是が非でも要件に合うものを期日までに量産化しなければならず、そのため新設備の導入の判断はモデル開発のスタートとほぼ同時期、2018年の3月に行われている。このことからも、相当な覚悟があったことが伝わってくるだろう。
3代目MT-09は2020年秋の伊ミラノショーで発表。対してスピンフォージドホイールはヤマハ初挑戦の技術にもかかわらず、2018年3月に設備導入を決断し、わずか約2年半後の2020年8月に生産ラインを稼働させている。そのスピード感には驚かされる。
“ひとつまみレベル”の微細な調整を繰り返した素材
このスピンフォージドホイールにおいて、設計や製造とともに重要なカギを握っているのが素材だ。ヤマハの社内には設立およそ40年になる材料技術部があり、ここでは鉄やアルミといった一般的な金属だけでなく、マグネシウムやチタン、さらには樹脂、ゴム、オイルなどの材料分析や開発を担っている。
「このスピンフォージドホイールに使っているアルミ合金は、従来の材料と熱処理で得られるものよりも強度は高いのですが、そのままだとしなやかさ(靱性)が足りないんです。そこにフローフォーミングを加えることで、リム部の靱性を復活させています」
【大島かほりさん(生産技術本部 材料技術部)】2014年入社。入社時から材料技術部でアルミ部品の分析や開発を担当。愛車はFZR250Rほか。
スピンフォージドホイールの材料開発を担当し、アルミブレンダーの異名を持つ大島かほりさんがそう教えてくれた。
MT-09の最高出力は120ps。それほどの大パワーを路面に伝えるホイールにしなやかさが必要なのか、などと疑問に思う人がいるだろう。だが、とくにリム部に関しては硬すぎると路面からの衝撃によって割れが生じやすく、そこからエアが漏れてしまうことも。つまり、ある程度の靱性が必要なのだ。
アルミ合金は、その名のとおりアルミニウムを主成分とする合金だ。スピンフォージドホイール用素材のベースとなったのはAC4CHと呼ばれる鋳造用のアルミ合金で、その化学成分はJISによって細かく決められている。添加されている合金元素は10種類以上で、もっとも多いのはシリコン(Si、ケイ素)の6.5〜7.5%。アルミ合金を1Lの牛乳パックに例えると、シリコンの含有量は80mlで、およそヤクルト1本分だ。そして、次に多いのがマグネシウム(Mg)の0.25〜0.45%で、こちらは小さじ1杯分でしかない。
スピンフォージドホイール用のアルミ素材はAC4CHというJIS規格のものをベースに、フローフォーミングに適した特性を追求したヤマハの独自ブレンド。フローフォーミング後の熱処理時間や温度も新たに開発されたものだ。
スピンフォージドホイール用のアルミ合金は、おもにマグネシウムの量を独自に調整しているという。世界中にある基礎データを参考にしたとはいえ、フローフォーミングに適した割合を探るため、基礎研究の段階では0.05%刻みで試作を繰り返している。先の牛乳パックに例えるなら、0.05%はひとつまみに満たない分量だ。
付け加えると、金属組織を変化させて強度をコントロールする熱処理についても、AC4CH用とは異なるスケジュールになっているという。
【鈴木 康修さん(生産本部 PTアルミ技術部)】2002年入社。フレーム/ホイール鋳造の製造直接部門でヤマハ製スーパースポーツほぼ全車に携わり、その経験を買われ2014年に現部署へ異動。フレーム、ホイールの新機種生産準備を担当する。
「ラボには小さな電気炉があって、そこでは熱処理を細かくコントロールできます。しかし、現場では連続的に量産するので、どうしても試作品のようにはいかない。条件的にストライクゾーンがピンポイントなので、ここは最後まで苦労しましたね(大島さん)」
神田さんと同じアルミ技術部に所属する鈴木康修さんも「最適な熱処理を導き出すために、温度を5℃刻み、時間を5分刻みで実験するなど、強度が出るまでは気が遠くなるような総当たり戦でした」と、その苦労を振り返る。
3本や6本も検討し、最終的に選ばれたのが10本スポーク
MT-09のホイールは、初代と2代目が共通で、3代目でスピンフォージドホイールを初採用。最新の4代目もこれを継続している。実のところスポークの本数だけで言えば、初代から10本で変わらないのだ。
アルミキャストホイールは、軽さを優先するなら3本の中空スポークがもっとも有利だという。その証拠に、ヤマハの1000ccスーパースポーツの歴史を振り返ると、1987年に登場したFZR1000からYZF1000Rサンダーエースを経て、2002年の3代目YZF-R1までが3本スポークホイールを採用しており、このデザインが当時のベストであったことが分かる。
「キャスティング(鋳造)で作るなら、軽さにおいて3本の中空スポークが有利なんですけれど、どうしてもスポーク間のスパンが広くなるので、この部分のリム剛性は不利になってしまう。そこで、2000年をすぎたあたりから多スポーク化が進んだ印象ですね(香島さん)」
スピンフォージドホイール開発中のデザイン案。左から、2本並んだスポークのリム側を広げたもの/スポークが並行/リム側を狭めたもの。わずかな違いではあるが、並べると印象がずいぶんと異なる。
【山口昌也さん(機能モジュール開発部ホイールG チームリーダー)】2004年入社。ボディ部品を担当し、スイングアーム、燃料タンク、ホイールといった重要保安部品を歴任。その過程で培った構造解析の知見を活かし、現部署では教育・業務効率改善も推進する。
スピンフォージドホイールをデザインするにあたり、3本や6本スポークも検討。最終的に選ばれたのが現状の10本である。同じ10本スポークでもMT-09の初代や2代目とは異なり、隣り合った2本のスポークがリムに向かってややすぼまったようなデザインとなっている。
「これは停まっている状態でも動きを見せたいということで、このデザインを選びました。開発の段階では2本のスポークを平行にしたり、逆に開いているようなものも検討しています。シミュレーションによると、スポークを平行にした方がハブとリムを最短距離で結べるので、ホイール1本あたり10gほど軽くできるのですが、ここはあえてデザイン優先としました」
スピンフォージドホイールの設計の礎を築いた山口昌也さんは、そんな裏話を教えてくれた。
より軽くできるスポークアレンジがあると分かっていながら、あえて躍動的なデザインを選択した開発メンバー。それでもなお、前後合わせて従来比でおよそ700gもの軽量化に成功しているほか、リム部の最小厚さは3.0mmから2.0mmとなり、慣性モーメントは10%もダウンしているのだ。
ホイールリムのカットモデル。上が1/2代目MT-09用で、下が3代目MT-09のスピンフォージドホイール。リム部の薄さは一目瞭然だが、ホイール端のフランジ部分が薄いことにも注目。
3代目MT-09のスピンフォージドホイール(右。左は1/2代目MT-09)は、リム部だけでなくハブの形状でも軽量化を追求。より有機的な形状となり、肉抜き穴も大きくなっていることが分かる。
機能を純粋に追求し、普遍性のあるデザインが生まれる
【安田将啓さん(プロダクトデザイン部CVG グループリーダー)】2008年入社以来、商品企画・デザイン企画業務に従事。2/3代目MT-09、3代目トレーサー9、2代目XSR900、NIKEN、現行XMAXなどのデザイン企画業務を担当。愛車は現行型XSR900。
スピンフォージドホイールの話からはやや逸れるが、ホイール自体のデザインについても触れておきたい。当然ながら、ホイールデザインは車両全体とのマッチングが重要だ。これに関して、3代目MT-09のデザインを担当した安田将啓さんは次のように語る。
「3代目MT-09では“機能のための最低限の外観”を意識しています。そのためヘッドライトや燃料タンク、排気チャンバーなどは極力エンジンに寄せてマスを集中させつつ、それ以外の部分、シートやホイールなどは極力ミニマムに作ることで“塊感と抜け感”を対比させたいと考えました」
そのため、ホイールのデザインは求められる要素をミニマムに満たす、機能的な形が追求されている。デザインのためのデザインではなく、魅力的な機能を純粋に突き詰めていった先にある形を求めていったという。
エンジンを中心とした排気系や燃料タンクの塊感に対し、それ以外の部分はできる限りミニマムに…というのが3代目MT-09のデザインコンセプト。スピンフォージドホイールもこの方針の中でデザインされている。
それを裏付けるエピソードがある。3代目MT-09で登場したスピンフォージドホイールは、その派生モデルであるトレーサー9GTや2代目XSR900/同GPにも使われている。しかし、ホイールのデザインを行っている時点で、トレーサーやXSRの車体デザインはまだ決定していなかったのだという。
「もちろんホイールをデザインしながら、トレーサーやXSRにも使うことを意識していたのですが、結果的にそれら派生モデルの車体デザインと合わせても、違和感なくこのホイールを収めることができた。機能に純粋な形であれば、デザインの異なるモデルと組み合わせても違和感は生じないんです」
(左上から時計回りに)、2021年モデルのMT-09(3代目)/同じく2021年モデルのトレーサー9 GT/2022年モデルのXSR900/2024モデルのXSR900 GP。それぞれデザインの方向性は異なるが、どのモデルもスピンフォージドホイールを履きつつ、そのマッチングには破綻がない。
スピンフォージドホイールのために新たな設備を導入
スピンフォージドホイールを量産するにあたっては、新たにフローフォーミングマシンと熱処理炉が導入されている。
フローフォーミングの工程では、まず金型に離型剤が吹き付けられ、セットされたホイールが高速で回り始める。側面のリム部が大きな炎によって炙られ、表面温度が300〜400℃に達すると、ローラーが圧延を開始する。その動きは陶芸のろくろのようであり、リム部が少しずつ引き延ばされていくさまは見ていて飽きない。
ちなみにMT-09のリヤホイールの場合、圧延のためにローラーを押し当てる回数は、センターのスポーク部を避けつつ上側と下側で異なっている。重力鋳造で溶湯が固まるプロセスが上下で異なり、アルミの組成に差が生じるため、それを考慮した加工回数が設定されているのだ。普通に考えれば上下の圧延回数は同じになりそうなものだが、これも試行錯誤の結果から導き出されたものだ。
金型へと流し込む。スピンフォージドホイール本体の鋳造方法は重力鋳造で、成形直後のリム部には溶湯(=溶けたアルミ)に圧力をかけて空洞の発生などを防ぐ”押し湯”と呼ばれる部分が残る(このカットのみヤマハ公式YouTubeより)。
リムをバーナーで炙りながら、左側に見えるローラー(矢印部)で圧延していく。圧延されるのはスポークがつながる部分を挟んで左右方向で、写真では上下方向にリムが引き伸ばされていく。
フローフォーミングを終えた直後のリム。高温と強い圧力を加えられ続けた痕跡がなんとも生々しいが、この後の機械加工工程で綺麗に切削される。
フローフォーミングを終えたホイールは、AGVと呼ばれる無人搬送車に載せられて、熱処理工程へと運ばれる。新たに導入された巨大な熱処理炉は、内部がタワーパーキングのようになっており、部屋の数はなんと112個もある。その各部屋に1本ずつホイールが収められ、500℃以上でおよそ2時間の熱処理が行われる。これまでは10〜20本のホイールがまとまらないと熱処理が行えないバッチ式であったことから、かなり生産性が上がったことになる。
以前の記事でも紹介したAGV(左)はスピンフォージドホイール工場でも活躍。フローフォーミングを終えたホイールは熱処理炉(右)に搬入されて熱処理を行い、その後に機械加工工程へと回される。
新しい熱処理炉は内部が小部屋で仕切られており、先に投入されたホイールの熱処理を行いながら、新規のホイールを後から投入していけるのも特徴。この規模の設備を新規導入している点からも、スピンフォージドホイールにかけるヤマハの想いが伝わるはずだ。
【取材後記】内製だから達成できた業界最軽量級ホイール
トルク&アジャイルをコンセプトに進化し続けるMT-09。その3代目の足まわりを初めて見たとき、切削加工された美しいホイールに目を奪われた。まるでアフターマーケットの鍛造品のようなホイールが純正採用される日が来るとは。そして、そのホイールがトレーサー9 GTやXSR900、XSR900GPといった、まったく異なるスタイリングの機種に次々と採用されてなお、違和感なく溶け込んでいることは称賛に値しよう。
設計部門、製造部門、そして材料部門が三位一体となって達成できた大きなブレイクスルー。ユーザーにとって何よりうれしいのは、これだけ高品質なホイールを採用しながら、車両自体の価格が大幅にアップしていないことであり、この点においてもスピンフォージドホイールが業界に与えたインパクトは大きいと言えるだろう。
<ヤマハ発動機 公式YouTube>YAMAHA MOTOR CRAFTSMANSHIP〈ヤマハの手〉~SPINFORGED WHEELのご紹介~
※本記事はヤマハ発動機が提供したもので、一部プロモーション要素を含みます。※掲載内容は公開日時点のものであり、将来にわたってその真正性を保証するものでないこと、公開後の時間経過等に伴って内容に不備が生じる可能性があることをご了承ください。※特別な表記がないかぎり、価格情報は税込です。