【感動創造工場“ヤマハの手”Vol.3】2輪生産部門の頂点・本社工場「自動化と匠の技を融合し、最高のヤマハ車をアセンブルする」
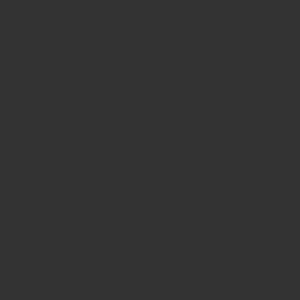
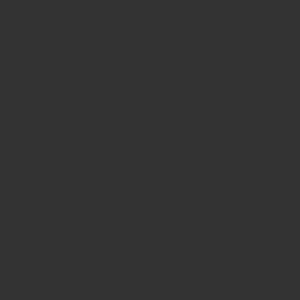
世界広しと言えども、ヤマハ発動機ほど作り手が“アツい”2輪メーカーもないだろう。細部まで徹底的に作り込まれ、こだわりを訪ねようものなら技術者の話はとどまることを知らない。そのすべては“ユーザーに感動を与える最高の製品を”という、ヤマハの企業理念「感動創造」に起因するものだ。その感動を工場から送り出し続ける、製造技術者たちの奮闘にスポットを当てる短期集中連載、第3回は本社工場における車両組立を紹介する。
●文:大屋雄一 ●写真:山内潤也 ●BRAND POST提供:ヤマハ発動機
各国の手本となるマザー工場・磐田ファクトリー
2024年10月現在、ヤマハ発動機は世界各国に2輪の生産拠点を有しており、その多くが需要伸長の著しい東南アジアに集中している。2023年、ヤマハが全世界で製造したのはおよそ479万台。もっとも生産台数が多かった国は、YZF-R25やXMAXなどを手かけているインドネシアだ。これに続くのはインドとベトナムで、この三カ国だけで過半数ものヤマハ車を生産している。
さて、日本におけるヤマハ車の生産拠点は、静岡県磐田市にある本社工場で、昨年はおよそ21万台を製造している。全生産台数479万台のうちわずか4%ではあるが、ここでは高付加価値製品に絞った多品種少量生産が行われており、国内はもちろん、欧州や北米などの先進国を中心に出荷されている。
この本社工場で生産されているのは、スーパースポーツのYZF-R1やR6、話題沸騰のXSR900 GPを抱えるCP3シリーズ、フロント2輪のナイケン、オフロード競技モデルのYZシリーズなどだ。さらに、日本ではすでにディスコンとなったSR400やセロー250、TW200なども輸出専用車として現在も生産されており、そのラインナップはとても幅広いのだ。
世界各国にあるヤマハの生産拠点の中でも、これだけ多くのモデルを手かけているのは本社工場以外になく、ゆえに各国のお手本とも言うべきマザー工場としての役割も担っている。これからご覧いただくのは、まさにヤマハ2輪の生産部門の頂点に君臨する「磐田ファクトリー」なのだ。
これぞ産業革命! ロスなく小ロットを作れる「超汎用ライン」
スーパースポーツ/クルーザーなど、車種専用のラインで生産していた時代の本社工場(写真は2019年頃)。
もの作りの現場が好きな人なら、動画サイトでバイクが作られる様子を一度は視聴したことがあるだろう。車両の両脇に立つ作業者が次々とパーツを組み込んでいき、バイクの姿形が徐々に現れる様は見ていて飽きないものだ。ベルトコンベアの手前から奥までずらりと同一機種が並ぶ風景は圧巻であり、誰もがイメージするバイクの組立工場はこれであろう。
ヤマハの本社工場も、このベーシックな生産方式を採用していた。具体的には、MTシリーズやYZシリーズ、スクーター、スーパースポーツなど、ジャンルごとに最適化された生産ラインが4本あり、最低台数40台を1ロットとして稼動していたのだ。
このようにジャンル分けをすることのメリットは、たとえばMT-09のあとにMT-07を作ろうとした際、使用する工具の入れ替えが最小限で済むことが挙げられる。こうした事前の準備は「段取り」と呼ばれ、トータルでの生産時間の長短に直結する。
【友田祐介さん(組立技術部 組立合理化G BDチームリーダー】2002年入社。生産ラインで車両組立を担当後、ライン合理化や設備導入、海外支援に従事。組立工場で構造改革や設備/治工具導入を担当した後、2023年より生産ラインの設計を担う現職に。
一方、デメリットとしては、販売会社からのオーダーが20台であっても、1ロットの最低台数である40台を作らざるを得ず、残りの20台は在庫になってしまうことだ。また、保安部品のないシンプルなYZシリーズと、電子デバイスを数多く装備したスーパースポーツとでは、工数に大きな差が生じるため、ラインごとに生産時間を平準化しにくい点も指摘されていた。
「それらの問題を一気に解決するため、取り組んだのが組立工場の構造改革です」
そう答えてくれたのは、組立合理化グループの友田祐介さんだ。
冒頭で触れたように、本社工場では高付加価値製品に絞った多品種を生産している。よりタイムリーにお客様へ商品を供給するため、構造改革のテーマとして次の3つが掲げられた。
- どのモデルでも組み立てられる超汎用ライン化
- すべてのモデルを毎日生産できる小ロット化
- 小ロットでもロスなく生産できる段取りゼロ化
40台を1ロットとする従来のベーシックな生産方式と比べると、にわかに信じられない目標だ。ゆえに根本的な発想の転換が求められた。黒電話から一気にスマホへ。それほどの大改革と言ってもいい。カギを握るのは、AGV(Auto Guided Vehicle)と呼ばれる無人搬送車と、パーツを運搬するトヨタL&F社製の「キーカート」。そして、それらを自走させるための徹底したDX(デジタルトランスフォーメーションの略。デジタル技術を活用して業務の改善や変革を行うこと)化だ。
工場内を無人で走行する“AGV”
本社工場内をバイクを載せて走り回るヤマハ内製の無人搬送車・AGV。重量は700kgで、電動モーターで自走する(最高速度は30m/分)。作業者の高さに応じてバイクを昇降させるリフターや、障害物を検知すると自動停止する機能も持っており、走行中に無線給電するため充電作業も不要。135台が稼働中だ。
AGVの部品搬送版“キーカート”
1ロットの最低台数は、40台からなんと4台に
フレームやエンジンを載せたAGVと、必要なパーツが並べられたキーカートは別々のエリアからスタートし、床に貼られた磁気テープをトレースしながら、新設された「超汎用組立ライン」へ同時に進入する。
これだけでも新鮮な光景だが、驚きはまだ続く。AGVの前方にはIDタグがあり、ラインの下部に設けられたリーダーがそれを読み込むと、その車種に応じて電動締め付けツールのトルク値や、各油種の注入量が自動的に変更されるのだ。従来の専用ライン方式では、各モデル毎に別のツールに交換したり、注入量を作業者が手動で変更していたので、段取りに必要な時間が一気に短縮されたのだ。
超汎用ラインに到達したAGVは一列に並び、連なってライン内をゆっくり進んでいく(そのため、ここだけ見るとベルトコンベア風)。その両脇には部品を積んだキーカートがやはり一列に並び、AGVに併せて前進する。
左の白いカードがAGVに装着されるIDタグ。ここに収められた車種情報を右のリーダーが読み取って段取りを自動変更する。AGVはWi-Fi機能も搭載しており、システムからの指示でルートの切り替えやリフターの昇降も可能だ。
付け加えると、モデルごとに異なる生産負荷の差については、前後で2本あるラインのうちの後半を端折ったり、セルと呼ばれる作業ステーションを増減させる方法で対応している。こうした大改革により、ひとつのラインで工数の異なるさまざまなモデルを生産することが可能となったのだ。
「生産ラインは従来の4本から2本に集約することができ、1ラインあたりの生産モデル数は15モデル1カテゴリーから、17モデル3カテゴリーと増やすことができました。さらに、1ロット4台〜というハイサイクル生産によって、お客様へ最速でデリバリーすることが可能となったのです(友田さん)」
(左)カテゴリー別&1ロット40台のため、小回りの効きにくい従来ラインに対し、超汎用ラインでは65〜1000ccまでのモデルを同一ラインで生産可能としている。工数の異なる機種を同一ラインに流すには組立時間を均等に調整する必要があるが、これは2つのメインラインに加えて「セル」と呼ばれる作業ステーション(おもに外装を装着する)を複数用意し、工数の少ない機種は2本目ラインやセルをスキップすることで吸収(右)。IDタグの情報を基にフレキシブルに動ける、AGVならではの組立方法だ。
左の従来生産(専用ライン)方式では、たとえば図内のFというモデルでは、月曜日に39台作ると次の生産まで7日も間が空いている。これが右の現行方式(超汎用ライン)となるとすべてのモデルを毎日、少しずつ作れるため、組立者が作業を忘れにくくなり品質の安定にもつながる。超汎用ラインはタイムリーな生産以外にもメリットがあるのだ。
AGVやキーカートが誰の手も借りずに工場内を移動する光景は、なんとも不思議な光景だ。しかし、SF小説で描かれるようなディストピア感は一切漂っていない。その最たる理由は、バイクのアセンブルがすべて人の手によって行われているからだろう。
AGVの両側に立つ作業者は、キーカートで運ばれてきた部品を搭載したマーシャル台車から必要なパーツを選択し、流れるような動きで車体に組み付けていく。部品には必ず公差があり、組み付け方次第で乗車時のフィーリングが変わってしまうことも。予期せぬ状況に応じてアジャストできるのが匠の技であり、小さな気付きが改善へとつながるケースもある。こうして人の手によって組み上げられた製品は、最終工程の完成検査へと歩を進める。
無人搬送車が係留される場所に作業員はほぼ不在で、チャイムとともにAGVやキーカートが持ち場へ移動していく様子は未来感満載…なのだが、そこはかとなくお掃除ロボット的な愛嬌も。
しかし、超汎用ラインに移れば作業員が主役。AGVは彼らが作業しやすいよう、工程ごとに載せている車体を上下&回転させるなどして作業員をサポートするが、これはIDカードやWi-Fiで送られてくる情報に基づき自動で行われる。また、部品は組み立てる車体&工程に合致したものをその都度キーカートが運んでくるため、部品の組み間違いも生じない。
無資格者による完成検査は物理的に不可能
組立工場の最終工程において、適法性や商品性に問題がないかを最終確認するのが完成検査だ。公道を走行するバイクや自動車に対して国では安全基準を設けており、メーカーはそれに合致していることを証明する必要がある。ユーザーに渡る前の“0回目の車検”が出荷前に行われていると考えていい。
2018年、この大切な完成検査において、いくつかの自動車メーカーによる不正が明るみとなった。中でも多かったのが、完成検査員に任命されていない者による合否判定、いわゆる無資格検査だ。
この一件により、国土交通省は各メーカーに対して再発防止策を講じるように通達。これを受けてヤマハは、YFIA(ヤマハ・ファイナル・インスペクション・オートメーション)というシステムを構築した。これは従来の紙ベースだった検査表をデジタライズ化したもので、いつ、どのバイクを、誰がチェックしたのか、データとして残せるのが最大のポイントだ。
中でも「誰が」の部分はとても重要であり、なりすましや無資格検査の温床になりやすい。ヤマハはそうした不正を防ぐため、腕時計タイプの生体認証ウエアラブルデバイスを着用した人物しか、完成検査を行えないシステムを導入している。
【吉田晃規さん(LM品証品質監理部 完成検査2Gr グループリーダー)】2006年入社。品質保証部 評価解析Grでのスノーモービルやバギーのテストライダーなどを経て2016年にはブラジルへ出向。2023年より生産ラインの導入準備やルール作りを担う現職に。
このデバイスは脈拍と指紋によるダブルの生体認証システムで、バンドを外した瞬間に設定がリセットされる。つまり他人への貸し出しは不可能であり、無資格者に仕事を手伝ってもらうことはできないのだ。
「ここまで厳格にすることが、我々の“絶対に不正を行わない”という強い意志です」
そう教えてくれたのは、完成検査2グループのグループリーダー、吉田晃規さんだ。
日本では、250ccを超えるバイクに車検が義務付けられている。車検制度が存在する国は他にも存在するが、その内容は世界的に見ても日本だけが突出して厳しい。
「今のところYFIAに対応しているのは日本向けのみですが、いずれ輸出モデルもこれに移行しようと思っています(吉田さん)」
これがリストバンド型の生体認証システム。指紋と脈拍から検査員を認識し、これを機械にかざすことで完成検査が実施できる。手首から外すと無効化されるため“なりすまし”は物理的に不可能だ。
完成検査は、生産された車両すべてに対して実施される。いわゆる全数検査だ。冒頭でも触れたが、ここ本社工場の生産台数はおよそ21万台。全体の4%とはいえ途方もない数である。
その完成検査に携わっているのは、付帯作業者を含めて現在40数名。検査員には初級、中級、上級とランクがあり、一番下の初級でも登録されるまでに社内で半年の研修が必要だ。日本向けの完成検査が行える完成検査員は30数名配置されているが、最終判定が可能なのはその中の約2割のみ。長い実務経験を経て昇級できる上級検査員の資格に加え、国家資格の整備士免許が必要という、じつに狭き門なのだ。
わずかな時間で“官能”を検査する匠の技
AGVに載せられたままやってくる完成車は、検査エリアに着岸したあと、まずガソリンが注入される。その油種については、IDタグを通じて自動的に指示されるので、これも「超汎用組立ライン」化がもたらしたメリットのひとつだ。この先は“検査員”という人の手に委ねられるのは昔から変わらない。
検査レーンは3本あり、もっとも新しいレーン3のみ前後輪を同時に回せる2つのローラーを備えるが、検査できる内容はすべて共通だ。検査員はこのローラーの上で、エンジンの始動性やシフトフィール、エンジンノイズ、一定速度、全開加速、サイドスタンドのスイッチなど、車両の個体差や作動性に関する100〜150項目ものチェックを行っていく。それも30秒から長くても1分ほどの間にだ。
その動きはまるで楽器を演奏しているかのようにリズミカルで、ときおり検査員は奏者のごとく真剣な表情を見せる。ヤマハではこれを“官能検査”と呼んでいるが、わずかな時間で音やフィーリングの違いを見抜く検査員には、高いスキルが必要なのは想像にがたくないだろう。
官能評価では五感をフル活用して違和感をチェック。経験や技術が必要な、デジタル化は難しい高度な作業だ。ちなみに専用ライン時は同機種が複数台まとめて流れてくるため異常にも気づきやすかったが、超汎用ラインへの改修により、検査員にはどんな機種がいつ来ても対応できるスキルが求められることに。ここ数年の学び直しにより、今では多くの検査員が対応可能になっているという。とにかく“人の力”が要求されるパートなのだ。
その後、日本向けについては、ブレーキの制動力やスピードメーターの速度指示誤差、アイドリング時の排ガス、ヘッドライトの光軸などを確認。加えて、昨今は電子デバイスが増えていることから、OBD2を通じて各種センサーへの通電もチェックされる。
なお、トレーサー9 GT+については、ヤマハの現行車で唯一のACC(アダプティブ・クルーズ・コントロール)を採用しているため、ミリ波レーダーの照射方向のキャリブレーションも実施される。システム的には走行中に自動補正されるので、これを行わなくてもとくに問題ないのだが、納車時から正しく機能してほしいという、お客様に対するヤマハの思いやりなのだ。
スピードメーターの誤差など、国交省が定める内容(車検と同等)に沿った検査を実施し機能面の検査は終了。トレーサー9 GT+では車体の前にボードを立ててミリ波レーダーを反射させ、照射方向の補正を行ってから出荷する。
こうした法的なチェックのあと、最後に行われるのは傷や凹みの確認だ。これもデジタライズが不可能なパートであり、合否判定は検査員の目に委ねられる。ヤマハ車として世に誇れる状態にあるか。これはもう官能検査のひとつといっても過言ではない。
【犬塚紳吾さん(LM品証品質監理部 完成検査1Gr 全数検査実施T 職⻑)】2007年入社以来、17年にわたって完成検査一筋。2017年に職場リーダーとなりベンチャーやVMAX、FJRなどの生産ラインを担当し、2022年からは人材教育なども担う現職に。
「部品や組み立ての精度が上がっているので、機能的な問題でNGになるケースは1000台のうち1台あるかどうか。多いのはやはり微細な傷ですね」
と語るのは、完成検査1グループの職長、犬塚紳吾さんだ。
この最終エリアは傷を発見しやすいように照度が決められており、車体の上部から下部、そしてリヤフェンダーの裏までくまなくチェックされる。検査員は傷の要因となりやすい名札や腕時計の装着が禁止されており、また先ほど説明した生体認証ウェアラブルデバイスもバンドは樹脂製となっている。
「モトクロッサーなどは、一度でもダートを走れば傷だらけになるのですが、それでもお客様の手に渡るときには美しくありたい。我々のこだわりですね(犬塚さん)」
傷や凹みのチェックも人間の技術に委ねられる作業。定量的な作業はシステム化を推進し、人はより定性的な分野に集中していく。ヤマハでは“人とシステムの共創”と呼んでいるそうだ。
【取材後記】大量生産品だがお客様には唯一。その想いが伝わる現場
こうして完成したヤマハ車は、ていねいに梱包されて清水港から世界中へと出荷される。作業者や検査員という匠の思いや技をつぶさに見てきたからこそ、これを受け取ったユーザーの笑顔が自然と目に浮かんでくる。
機械化やデジタライズが進んだからこそ、人でしかできないパートの重要性が際立っていると感じるのが、ヤマハの本社工場「磐田ファクトリー」だ。作業者が仕事に集中できるように、組立ラインの各所にスポットクーラーや大型ファン、ウォーターサーバーが設置されており、これらが間接的にヤマハ車の品質を高めていることは疑いようもない。
また、完成検査についても同様で、商品に対して最終的な責任を負っているという強い意志が現場からひしひしと伝わってくる。そして、ここをマザー工場として各国の生産拠点が学んでいるからこそ、世界中のヤマハ車が高い評価を受けているのだ。
今回、取材でお世話になった磐田ファクトリーのみなさん。中央はAGVをキャラクター化した「にょきにょき3兄弟(左)」の顔出しパネルで、社会科見学などで訪れる小学生に楽しんでもらいたいと作ったもの。そもそもこの「にょきにょき3兄弟」、協力会社の有志が描いたスケッチが元だそうで、そうしたアイディアを柔軟に受け入れる社風もヤマハらしさ? (そのgif動画を作っちゃうのもヤマハらしさ?)
<ヤマハ発動機・短編ドラマ>感動創造工場 Rev Factory はじまる【本編15分ver】
※本記事はヤマハ発動機が提供したもので、一部プロモーション要素を含みます。※掲載内容は公開日時点のものであり、将来にわたってその真正性を保証するものでないこと、公開後の時間経過等に伴って内容に不備が生じる可能性があることをご了承ください。※特別な表記がないかぎり、価格情報は税込です。