【感動創造工場“ヤマハの手”Vol.2】薄さ1.7mm!! XSR900 GPのCFアルミダイキャスト製フレームの生産技術に迫る
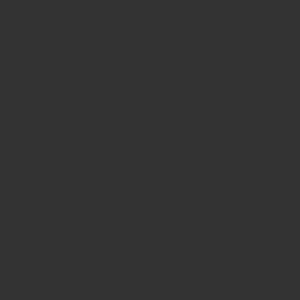
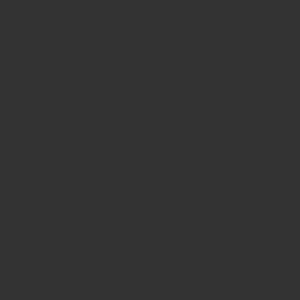
世界広しと言えども、ヤマハ発動機ほど作り手が“アツい”2輪メーカーもないだろう。細部まで徹底的に作り込まれ、こだわりを訪ねようものなら技術者の話はとどまることを知らない。そのすべては“ユーザーに感動を与える最高の製品を”というヤマハの企業理念「感動創造」に起因するものだ。その感動を工場から送り出し続ける製造技術者たちの奮闘にスポットを当てる短期集中連載、今回は新型XSR900GPのCFアルミダイキャスト製フレームに迫る。
●文:大屋雄一 ●写真:山内潤也/YM Archives ●BRAND POST提供:ヤマハ発動機
誕生から20年。CFアルミダイキャストは新たなステージへ
バイクのメインフレームに使われている素材はほぼ二択、スチールかアルミのどちらかだ。量産車に初めてアルミフレームが採用されたのは1980年代前半であり、100年以上におよぶバイクの長い歴史を振り返ると、フレームにアルミが使われはじめたのはつい最近と表現していいだろう。
フレームは、その名のとおりバイクの骨格であると同時に、ハンドリングをも左右する重要な機能パーツだ。アルミという新素材の登場によって、その形状はクレードルタイプからツインスパーへと発展。そして、外側へ露出した部分は、バイクの意匠の一部を担うこととなった。
そんなアルミフレームの可能性を信じて研究を続けてきたヤマハは、2002年に「CFアルミダイキャスト技術」を発表。翌2003年モデルのYZF-R6で、初めてこの新テクノロジーによるスイングアームとシートレールを採用した。設計やデザインの自由度が大幅にアップしたほか、シートレールについては先代のスチールパイプ製に対して大幅な部品点数の削減と軽量化に成功している。
あれから20年以上もの時が流れ、CFアルミダイキャスト技術はすでに新たなステージへと突入している。今回はその内容について紹介しよう。
【2003 YZF-R6】フレームの刷新や約9割の部品を新設計したエンジンなど、4年ぶりのフルモデルチェンジで2代目となったYZF-R6。CFアルミダイキャスト技術により、スイングアームは2.5mm、シートレールは2mmの最小肉厚を実現。フレームも含め、この3点をすべてアルミ鋳造化した量産2輪車はこの2003年型R6が世界初だ。
アルミ鋳造は“流し込む、押し込む、打ち込む”の3種類
アルミの比重はスチールに対して約34%と軽量で、しかも溶かした状態での流動性に優れることから、金属の中でも鋳造に適した素材として知られている。ヤマハはこのアルミの特徴を生かし、各製品にそれを織り込んできた。
【菅原佑太さん(CP3フレーム生産準備担当)】入社時からアルミ鋳造部門で第2世代CP3フレームの生産準備を担当。愛車はSR400。
そもそもダイキャストとは鋳造方法の一種で、溶かした非鉄金属の合金を金型(die)に圧入充填する製法だ。
「鋳造は、みなさんがイメージしやすいものに例えると“溶かしたチョコレートを型に流し込み、冷やして固めて欲しい形を手に入れる”という製法です。チョコなら27℃前後で溶け始めますが、これがアルミだと700℃ぐらいまで上げる必要があります」
そう教えてくれたのは、MT-09を筆頭とするCP3フレームの生産準備を担当した菅原佑太さんだ。
「アルミの鋳造方式には大きく3つあり、ひとつは重力鋳造です。これは溶けたアルミを上から流し込み、金型の隅々まで行き渡らせる方法で、中空構造の成型が可能です。その名のとおりアルミの重さだけで充填する方法で、フロントフォークのアウターチューブなどはこれで作られています」
「2つめが低圧鋳造です。LP(ロープレッシャー)鋳造とも呼ばれ、これは溶けたアルミ(溶湯)を金型の下部から上方へと空気圧を使ってじっくりと押し込む工法です。こちらも中空構造の成型が可能で、シリンダーヘッドなど、エンジンパーツの多くがLP鋳造で作られています」
「そして3つめが、今回の本題であるダイキャスト(高圧)鋳造です。油圧シリンダーを使って溶湯を高速かつ高圧で一気に金型へ流し込みます。イメージとしては、打ち込むとか射出するという感じです。人間の瞬きが0.1〜0.2秒と言われますが、それよりも短い時間で打ち込みます。薄肉成型に向いている製法で、鋳肌はきれいですし、寸法精度も出しやすいのが特徴です」
それぞれ3種類の鋳造方法では使う機械もまったく異なる。新幹線のごとく超特急で打ち込むダイキャスト(高圧)鋳造は中空構造は成形できないものの、他2種よりも高精度かつ薄肉成形が可能となる。
とはいえ、このダイキャスト鋳造が薄肉成型向きと言っても限界はある。フレームのような大物になると、表面積が大きい分だけスチール製の金型に熱を奪われ、充填途中でもあっという間にアルミが凝固してしまうのだ。また、射出前の金型内部には当然ながら空気が存在し、これを溶湯が巻き込んでしまうと製品に鋳巣と呼ばれる微細な空洞ができてしまう。この小さな穴が強度にも品質にも影響を及ぼしそうなことは想像にがたくないだろう。
これを解決したのが、ヤマハが2002年に発表した「CFアルミダイキャスト技術」だ。CFは「Controlled Filling」の頭文字で、日本語に訳すと「制御充填」となる。発表時の資料によると、1)金型真空度を向上させて空気抵抗を低減(従来比6倍)、2)金型温度の制御、3)溶湯の射出速度向上(従来比5倍)、4)離型剤の開発などにより、ガス混入量を1/5に削減できたという。そして、この技術で作られた代表的な製品のひとつに、2014年に発売された初代MT-09のメインフレームが挙げられる。
従来型の約半分、1.7mmの肉厚を実現する最新技術
MT-09は「トルク&アジャイル」をコンセプトに2014年に登場。翌2015年にはCFアルミダイキャスト製フレームや3気筒エンジンなどのプラットフォームを共有する形でMT-09トレーサーが、さらに2016年にはXSR900(初代)がリリースされている。
これら“第1世代”のCP3(クロスプレーンコンセプト3気筒)フレームによって価値あるプラットフォーム像の構築に成功したヤマハは、軽量/スリム/コンパクトという流れをさらに突き詰めるべく、第2世代となるCP3フレームの開発に取り組んだ。
“第1世代CP3フレーム”は初代MT-09で登場
2014年に登場した初代MT-09で登場した第1世代CP3フレーム。その後、クロスオーバーのMT-09トレーサー、ヘリテイジネイキッドのXSR900と矢継早にラインナップを拡充していった。
「プラットフォームを共有していますが、MT-09とトレーサーとでは要求される性能が相反しています。前者は峠道で意のままにスイスイと操れる上に、スロットルを開ければフロントが浮いてしまうような高い運動性能が求められます。これに対してトレーサーは、高速道路ではまっすぐ走ってほしいし、コーナリング性能もおろそかにできない。第2世代のCP3フレームは、こうした要件を両立するために、剛性を上げつつも軽量化という目標を掲げました。性能に妥協を許さない社風ですから、さらなる高みを目指したというわけです」
【脇本洋治郎さん(CP3フレーム開発担当)】MT-09/トレーサー9部品担当を経てCP3メインフレームを担当。 所有車はYZF-R25とトリッカー。
第2世代のCP3フレームの開発を担当した脇本洋治郎さんは、当時の開発シーンをそう振り返る。
「第1世代はMT-09を軸に据えていたので、バリエーションモデルを増やすにあたって限界を感じていたんです。そこで第2世代では、最初からラインナップ展開を要件に加えた上で、あとから剛性チューニングしやすいように設計しました」
「開発段階で鋳造技術グループからは“第1世代よりも薄肉にできる。2mm以下も可能だぞ”と聞いたのですが、最初は信じられませんでした。第1世代の最小肉厚が3.5mmですからね。それじゃあということで、従来比で厚さ半分を目標に開発を行った結果、フレーム全体で1.9kgも軽くすることができました」
そうして完成した第2世代のCP3フレームは、2021年発売の3代目MT-09でデビューした。当初の目標どおり最小肉厚は1.7mmとなり、これは第1世代の半分以下だ。100円硬貨(50円硬貨もそう)と同じ厚さであり、しかもそれは1か所ではなく、フレームの側面全体がほぼその厚さになっているというから驚きだ。
剛性を高めつつ軽量化も目指した第2世代
2021年、3代目MT-09で登場した第2世代CP3フレーム。左右のスパーをヘッドパイプとスイングアームピボット下でボルト結合する構造や、剛性確保のために裏側に立てられたリブなどは第1世代と同様だが、フレーム側面の最小肉厚が1.7mmという薄肉化により、大幅な軽量化を達成している。
「先ほど剛性チューニングしやすいように設計したと言いましたが、チューニングによってモデルごとにキャラクターを際立たせるには、土台となるフレームがしっかりしていないとダメなんです。3代目のMT-09を皮切りに、トレーサーやXSR900もこの第2世代のフレームにモデルチェンジし、それぞれがさらにマイナーチェンジしたり、バリエーションモデルを増やすなどしました。それだけ懐の深い骨格が作れたと自負しています」
「これが成功した要因のひとつに、アルミ鋳造の内製が挙げられます。そもそも、これだけ大きなものを外注に出したらコストが…というのもありますが、社内なので開発スピードが圧倒的に速い。何か問題が生じたらすぐに担当者に相談できますし、暫定の金型の段階から製造現場と密に開発を進められました。ちょうどいいタイミングで、鋳造技術グループからブレイクスルーとなる技術を提案されたのが大きかったですね」
第2世代CP3フレームは、2021年の3代目MT-09&トレーサー9GTの後、同年秋に2代目XSR900、そして2024年に4代目MT-09とXSR900 GPへと派生している。剛性チューニングが容易な構造として高い拡張性を実現しているが、そのキモとなるのが“内製”なのだ。
0.01秒を削るため“3倍速い”新型マシンを導入
【片貝寿幸さん(CP3フレーム生産準備担当)】PTアルミ技術鋳造技術1Gにてクランクケースの生産準備を担当する。
中途入社の片貝寿幸さんは、前職時代からアルミダイキャスト部品の生産準備に携わっている技術者で、だからこそ薄肉鋳造の難しさを肌で知るひとりだ。
「鋳造中、金型は閉じているので、その中を溶湯がどう流れているかは目視できません。ですので、溶湯挙動を流動シミュレーションで解析しながら最適な金型を作り込んでいます。どこから溶湯を入れて、どこから出すか。それは何か所あればいいのか。アルミにとって最良の経路を導き出すのが鋳造技術グループの仕事で、これはトップシークレットになります」
「続いては設備です。3つの要点がありまして、それは圧力と温度、そして速さになります。まず圧力ですが、溶湯が時速数100km/hで進むときの空気抵抗などを下げるため、金型内部に残っている空気をできる限りなくし、いかに真空に近づけられるかがポイントになります」
「次に温度について説明しますと、アルミがドロドロに溶けた状態がおよそ700℃で、成形が完了して金型から取り出すときが300℃ぐらいです。溶湯から伝わった熱により金型温度がが高くなりすぎると、化学反応でアルミが張り付いてしまうので、金型の内部には冷却水を流しています。それも凝固収縮を考慮した冷却回路を配置し、部位ごとに温度管理しているんですよ」
「そして、速さについては射出速度のことです。厚さ3mmの製品の場合、ダイキャストではコンマ1秒で固まるため、それよりも短い時間で射出する必要があります。弊社にある既存のダイキャストマシンでは0.07〜0.08秒ぐらいですね」
薄肉鋳造の秘伝中の秘伝が、金型の中をどのように溶湯が流れるかを解析するシミュレーションの技術。その上で圧力、温度、速さの“ダイキャスト3要件”を満足させられる設備やマシンの性能が必要となる。ちなみに、この第2世代CP3フレームにはヤマハが独自ブレンドした専用のアルミ材が使われている。前述した”秘伝”と併せれば、3Dスキャナーなどで形状だけ真似しても同じ性能を出すことは不可能という。
先ほど菅原さんから“射出速度は人間の瞬きよりも速い”と聞いたが、それが1/100秒の世界だったとは。フレームのように大きな部品を鋳造する金型に、そんな一瞬で溶湯を行き渡らせるなんて想像できないだろう。
「速いと思われるでしょうが、これが今までの一般充填と呼ばれる射出速度で、フレームぐらいの大きさだと最小肉厚で3mmぐらいが限界だったんです」
第2世代CP3フレームに求められる薄肉鋳造を達成するには、射出速度をもっと上げる必要がある。片貝さんによると、1.7mm厚の部分が凝固を始めるのは理論上0.06秒。すなわち、それよりも速く射出できければ可能となるのだ。
ヤマハは、それを達成するために新たなダイキャストマシンを導入した。既存のマシンに対して射出速度は3倍となり、アルミが液状になっている間に充填が完了する。その所要時間はわずか0.05秒。100分の数秒という、ほんの少しのタイムを削ることにも拘っているのだ。
もちろん、射出速度だけではない。金型には毎回、離型剤(アルミを金型から離れやすくする薬剤)を吹き付けているのだが、従来はこれが金型の冷却も兼ねていたため、1回につき希釈離型剤を1L以上も使用していた。これが新型マシンでは、金型内部の冷却が強化されたことで、従来の1/100以下の離型剤量で済んでいるのだ。離型剤は高温のアルミに触れるとガス化して鋳巣の原因になるので、少ないほど製品の品質が向上するのは言うまでもない。
アルミ鋳造部品の「大きさ」と「最小肉厚」の関係を製法別に示したグラフ。従来のCFダイキャスト(=ピンク色の部分)でも、従来の高圧ダイキャストと比べれば大きな部品をより薄く鋳造可能だったが、最新のCFダイキャストは、1mサイズの部品でさらに1mm程度の薄肉化を実現していることが分かる。ヤマハ入社前からアルミダイキャストに関わる片貝さんによれば「このサイズの部品で肉厚が2mmを切るのは業界的にもかなりチャレンジング」とのこと。
これは余談ながら、フレーム裏側に多数存在する直径1cmほどの円柱(赤矢印)は、部材を金型から抜く際に「押す」ための場所。部材がひずまず均一に抜けるよう、最適な数や配置(強度も必要なためリブが集中する場所に多く配置)がシミュレーションで導き出されており、重量増がミニマムで済むような形状や場所も検討されている。
GKが手かけた新ダイキャストマシンのカラーリング
ヤマハ本社工場・11号館で稼働中の新型ダイキャストマシン。写真奥の「CF+1」、手前の「CF+2」とそれぞれ名称されており、CF+1がおもにメインフレームやシートレール、CF+2がおもにクランクケースの鋳造を担当している。
最後に、この新しく導入された新ダイキャストマシンについて触れたい。
工場の一角に、白と青、そして黄色で彩られた巨大なマシンが2基並んでいる。ヤマハのレーシングカラーとのリレーションを感じさせる色使いだ。これが新たに導入された新型のダイキャストマシンであり、近付けば肌感覚でどこに熱源があるのかは分かるが、アルミを溶かすための炎はのぞき込まないと見えない。そう、熱さは感じるのに見た目はとてもクールなのだ。
この設備導入に携わったのは、海外拠点支援などを経験している熊谷広行さんだ。
【熊谷広行さん(生産現場リーダー)】低圧鋳造やダイキャスト鋳造の生産・生産準備、海外拠点の支援などを経て、2024年より生産現場のリーダー兼マネージメント補佐を担う。
「新しいマシンを導入するのはおよそ20年ぶりです。裏を返すと、今までは既存の設備を、製品設計や鋳造技術メンバーの創意工夫でうまく生かしてきたと言えるでしょう。私たち生産課のメンバーは、高い要求に対して現場を最適化し、お客様に対してバラつきのない高品質なものを作り続けることが大切だと考えています。そして今回、新マシンの導入にあたり、自分たちが誇りを持てる設備にしたいということで、GKデザイングループのひとつ、GK京都さんにご協力いただき、このようなカラーリングを採用しました」
ダイキャストマシンを美しくデザインしたからと言って、そこから生まれるバイクの性能や品質にはほとんど関係しないだろう。しかし、そこで働く、ヤマハを生み出す人々の意識やモチベーションは変化するはずだし、工場の設備や道具はいいものを作るための相棒。職人が相棒たる道具にこだわるのは当然だろう…というのがヤマハの考え方なのだ。
さらに、海外にもたくさんの生産拠点を持つヤマハにとって、ここは言わばマザー工場であり、世界中から鋳造技術を学びに研修生がやってくる。彼らがこのダイキャストマシンを見たとき、他の工場ではまず目にすることのない、洗練された鮮やかなカラーリングを持つその姿に圧倒されるに違いない。
CF+1/CF+2は黄色いアーム型ロボットを3台内蔵しており、離型剤の塗布や金型からの取り出し、鋳造時に生じる余分な部分の切断をNC制御で行っている。鋳造製品は時間や温度など、製造時の条件や環境を一定に保つことが品質の向上に繋がるが、そのためにこだわったのがこのロボットの制御とのこと。稼働開始日が記された看板からも、鋳造品質に対するヤマハの想いが伝わる。
この新ダイキャストマシンのカラーリングを決める際は、社員だけでなくその家族にもアンケートを実施。これは自分の親や家族が働いている職場に興味を持って欲しい…という意思の表れ。ちなみにヤマハでは年1回、創立月である7月に「ヤマハデー」という社内イベントを開催しており、社員の家族が工場やオフィスを訪れる。家族がヤマハの従業員であることに誇りを持ってもらうためにも”魅せる職場”の重要性は高いのだ。
取材後記:テクノロジー追求の根源にはお客様への想いがある
初代のMT-09を初めて目にしたとき、溶接痕の一切ないアルミフレームの美しさに驚いた人も多いだろう。CFアルミダイキャストの外観品質は明らかに高く、それでいて85万円を切る車両価格は、当時としてはインパクト大だった。
呼称こそ変わらないが、CFアルミダイキャスト技術は第2世代CP3フレームを皮切りに、次なるステージに入ったのは間違いない。それを声高にアピールしないのは、技術的にはこれまでの延長線上であり、その根源にある「お客様に最高の1台を」という想いが不変だからだろう。次はどの車種にこの美しい薄肉鋳造が採用されるのか、期待せずにはいられない。
左から脇本さん、菅原さん、片貝さん、熊谷さん。ヤマハが誇る高度な鋳造技術は、開発と製造という、2つの現場の総合力がもたらしているのだ。
【YAMAHA XSR900 GP】ヘリテイジ系ネイキッドのXSR900をベースに、‘80年代のGPマシン・YZR500を彷彿させるハーフカウルを装着。低めのセパレートハンドルや3代目TZR250R(3XV)を模したカウル固定方法など、かつてのレーサーレプリカ乗りの琴線をもくすぐる新ジャンルのヘリテイジモデルだ。足まわりや細部の造作などもGP専用とされている(車両写真:長谷川 徹)。
主要諸元■全長2160 全幅690 全高1180 軸距1500 シート高835(各mm) 車重200kg(装備) ■水冷4スト並列3気筒DOHC4バルブ 888cc 120ps/10000rpm 9.5kg-m/7000rpm 変速機形式6段リターン 燃料タンク容量14L ■ブレーキF=Wディスク R=ディスク ■タイヤF=120/70ZR17 R=180/55ZR17 ■メーカー希望小売価格143万円
※本記事はヤマハ発動機が提供したもので、一部プロモーション要素を含みます。※掲載内容は公開日時点のものであり、将来にわたってその真正性を保証するものでないこと、公開後の時間経過等に伴って内容に不備が生じる可能性があることをご了承ください。※特別な表記がないかぎり、価格情報は税込です。